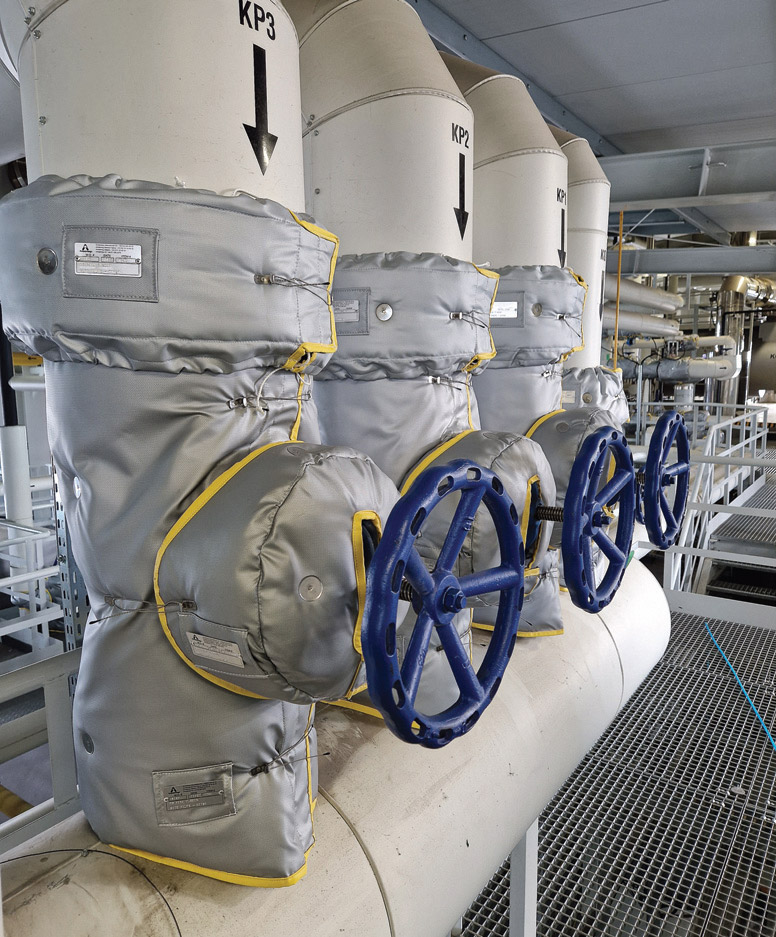
Zadanie jakie stoi przed przemysłem to zmniejszenie generowanej emisji gazów cieplarnianych. Oczywiście nie jest to możliwe do osiągnięcia z dnia na dzień. Energia odnawialna nie jest jeszcze opłacalnym rozwiązaniem zarówno z punktu widzenia kosztów, jak i dostępności. Nie ma wciąż wystarczającej jej ilości, a ponadto przejście całej branży przemysłowej na odnawialne źródła energii przeciążyłoby obecną infrastrukturę sieciową i jeszcze bardziej podniosłoby koszty. Deficyt i niska efektywność „zielonej energii” sprawiają, że niezwykle ważnym czynnikiem są procesy związane z obecnym użytkowaniem ciepła w każdej fabryce. Spora część zakładów przemysłowych została bowiem zbudowana kilkanaście lub kilkadziesiąt lat temu, a to stwarza ogromne możliwości zminimalizowania ciepła odpadowego i optymalizacji wydajności w ramach obecnych ich procesów. Chodzi o to, by zminimalizować straty energii w zakładzie, zoptymalizować jego efektywność energetyczną, a następnie zbudować strategię całkowitej dekarbonizacji. W tym kontekście przemysł wykorzystujący wysokie temperatury w procesie ma chyba największe pole do popisu. Przyjrzyjmy się zatem co możemy zrobić w ramach oszczędności energii. Skupmy się na najprostszych i najłatwiejszych rzeczach do wdrożenia od zaraz.
W OCZEKIWANIU NA OPŁACALNĄ I CZYSTA ENERGIĘ
Wraz z rozwojem technologii obserwujemy niewiarygodny postęp i modernizację w przemyśle. Innowacje sprawiają, że maszyny zastąpiły człowieka na różnych etapach produkcyjnych, a wiele zautomatyzowanych procesów nie wymaga stałej uwagi personelu. Niestety, praktycznie wszystkie branże i gałęzie przemysłu nie mogą spocząć na laurach i zobowiązane są do podejmowania kolejnych wyzwań. Takim wyzwaniem jest osiągnięcie zerowej emisji netto, czyli zrównoważony rozwój środowiskowy. Obecnie tysiące zakładów na całym świecie codziennie emituje olbrzymie ilości gazów cieplarnianych, a wiele z nich poczyniło niewielkie postępy w osiąganiu swoich celów w zakresie ich redukcji. Przyczyną tego stanu rzeczy jest wciąż oczekiwanie na nowe, czyste i opłacalne ekonomicznie odnawialne źródła energii, które do tej pory nie zostało zastosowane.
Można w tej sytuacji czekać z założonym rękami albo już teraz optymalizować to co mamy i z czego korzystamy. Racjonalnym rozwiązaniem jest oczywiście szukanie oszczędności w zużyciu energii i redukcji emisji już teraz, a pole do tego typu optymalizacji występuje niemal w każdym polskim zakładzie.
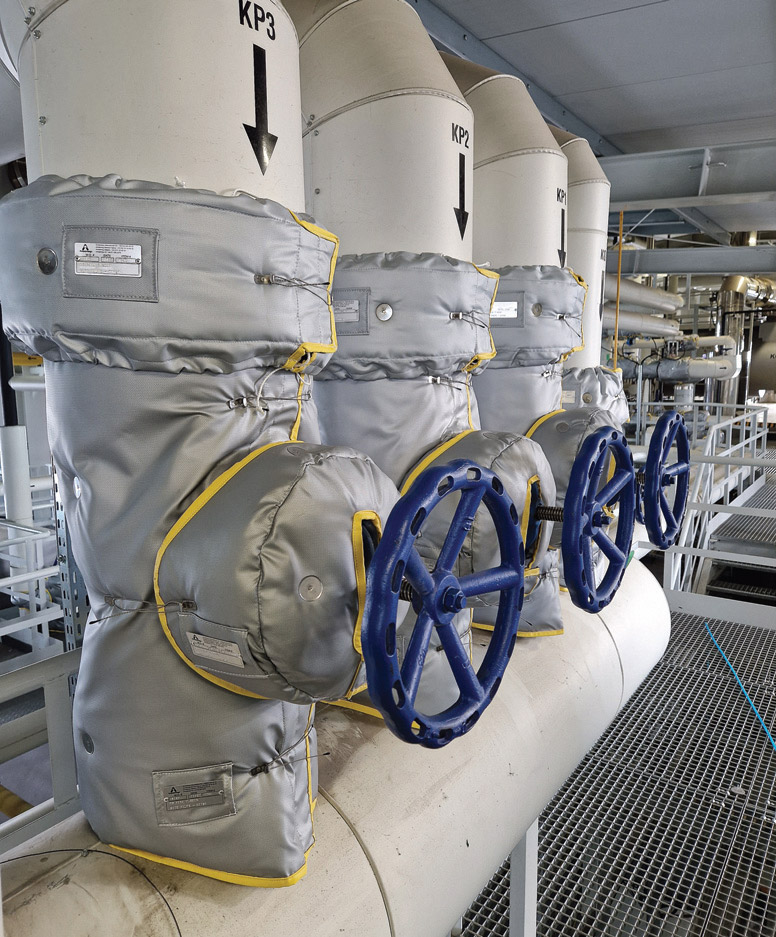
Rysunek 1. Termoizolacja zaworów odcinających
UZUPEŁNIANIE IZOLACJI NA ARMATURZE I GORĄCYCH POWIERZCHNIACH
Każdy zakład przemysłowy to setki metrów rur, które muszą być w odpowiedni sposób zaizolowane, by nie tracić zbędnej energii na skutek wymiany ciepła. Inaczej mówiąc, by energia, która ma trafić do miejsca docelowego, nie była po drodze tracona. Izolacja termiczna to prosty i skuteczny sposób na podniesienie efektywności sieci cieplnych. Ważne, by izolacja była o niskim współczynniku przenikania ciepła oraz miała odpowiednią warstwę ochronną przed uszkodzeniami mechanicznymi lub oddziaływaniem środowiska.
O ile zakłady przemysłowe pilnują, by rurociągi były zaizolowane, to często zapomina się o możliwości uzupełniania termoizolacji na zastosowanej armaturze. Stosując termoizolację na zaworach istotne jest, by była ona w łatwy sposób demontowalna, trwała i nie komplikowała życia służbom utrzymania ruchu. Rysunek nr 1 przedstawia parowy kolektor z zaizolowanymi zaworami odcinającymi. Co warte odnotowania, pokazane termoizolacje są ściśle dopasowane do zaworów nie tworząc mostków powietrza, co zwiększa oszczędność ciepła.
Na rynku spotkać można wielu producentów termoizolacji. Najlepsze z nich zaprojektowane są w technologii CAD i wyprodukowane w technologii CNC (z ang. Computerized Numerical Cotrol). Wszystko po to, aby niestandardowe izolacje armatury były perfekcyjnie dopasowane do izolowanych powierzchni, w celu oszczędzania energii, wychwytywania promieniowania cieplnego, minimalizowania konserwacji izolacji i poprawy otaczającego środowiska pracy. Izolacje powinny przy okazji być elastyczne, łatwe w montażu, demontażu i ponownej instalacji, umożliwiając szybki dostęp i łatwe serwisowanie sprzętu. Typowe zastosowania izolacji termicznych obejmuje zawory grzybkowe, kulowe, regulacyjne, zwrotne i przepustnice, a także kołnierze, pompy, oprzyrządowanie, głowice urządzeń, drzwi kotłów parowych i wszelkie złożone powierzchnie trudne do zaizolowania metodą tradycyjną.
Rozważmy przy okazji inwestycji jak będzie wyglądał ewentualny demontaż i ponowne jej założenie, czy izolacja wiązana jest zwykłymi sznurkami, czy ma rzepy i system pasów mocujących. Czy jest trwała? Wszak chcemy ją użytkować przez kolejne lata. Nasuwa się także jeszcze jedno pytanie. Kiedy rozważać zakładanie izolacji? Inaczej mówiąc, od jakiej temperatury procesowej ma to sens? Oczywistym jest, że im wyższa temperatura tym większe oszczędności ciepła. Izolacja na armaturze parowej i ta montowana na instalacjach oleju grzewczego nie podlegają więc dyskusji. Warto wziąć również pod uwagę armaturę na kondensacie i na procesach związanych z wodą gorącą powyżej 100°C.
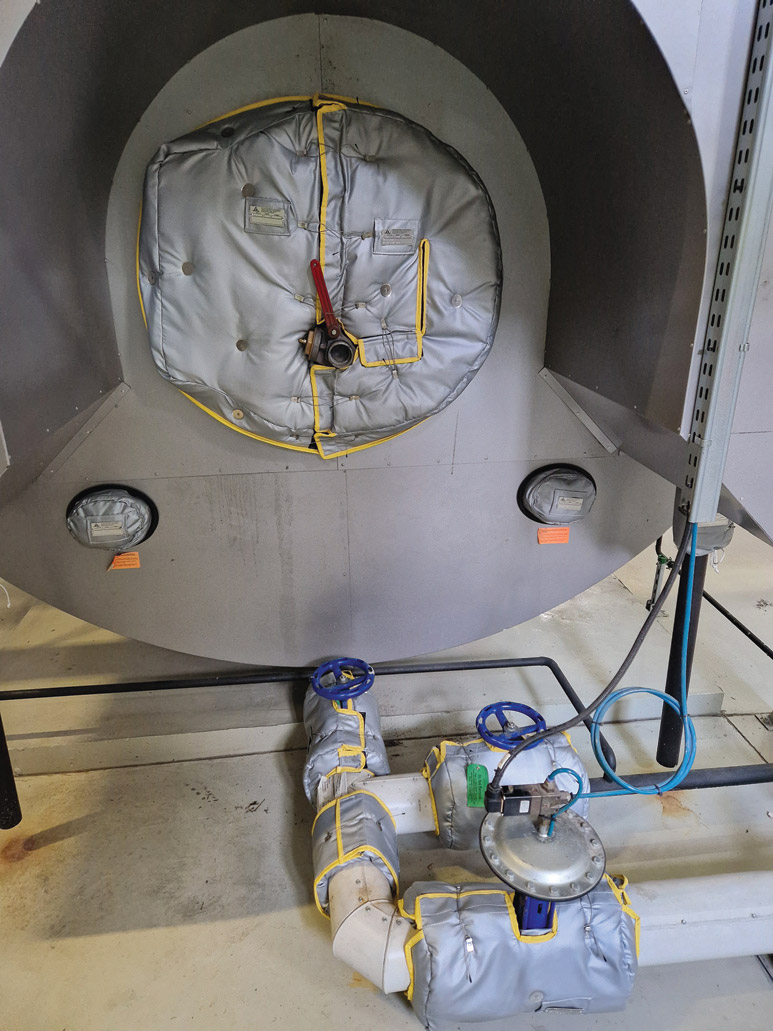
Rysunek 2. Izolacja kotła parowego
Dzisiejsze ceny energii sprawiają, że koszt zwrotu inwestycji w postaci uzupełniania izolacji na armaturze jest niesłychanie szybki i oscyluje przeważnie w granicach 6-11 miesięcy. Powyższy czas zwrotu inwestycji nie uwzględnia białych certyfikatów (świadectw efektywności energetycznej), które można również dla tego typu inwestycji pozyskać. Finalnie, termoizolacje armatury potrafią się same sfinansować dzięki pozyskaniu Świadectw Efektywności Energetycznej z Urzędu Regulacji Energii. Zatem można wysnuć oczywisty wniosek, że warto zwrócić uwagę na jakość wykonania i aspekt użytkowania termoizolacji.
Zakłady parowe, w których praktyka regularnej diagnostyki odwadniaczy nie istnieje narażone są na około 40% uszkodzonych odwadniaczy
KONTROLA SZCZELNOŚCI INSTALACJI
Mówiąc o oszczędności energii niezwykle ważna jest regularna kontrola szczelności instalacji. Krótko mówiąc, czy przypadkiem nie tracimy energii na przesyle lub w wyniku uszkodzenia urządzeń zamontowanych w naszych sieciach energetycznych. Szczególnie dotyczy to zakładów wykorzystujących parę jako nośnika energii, gdyż duże straty mogą generować urządzenia odpowiedzialne za odprowadzanie kondensatu z pary, czyli odwadniacze. Rozwiązania mamy dwa: zlecać regularną diagnostykę odwadniaczy lub wdrożyć strategiczny plan zarządzania odwadniaczami.
Rysunek nr 3 przedstawia jak częstotliwość diagnostyki odwadniaczy może wpływać na ich awaryjność, a tym samym na straty energii.
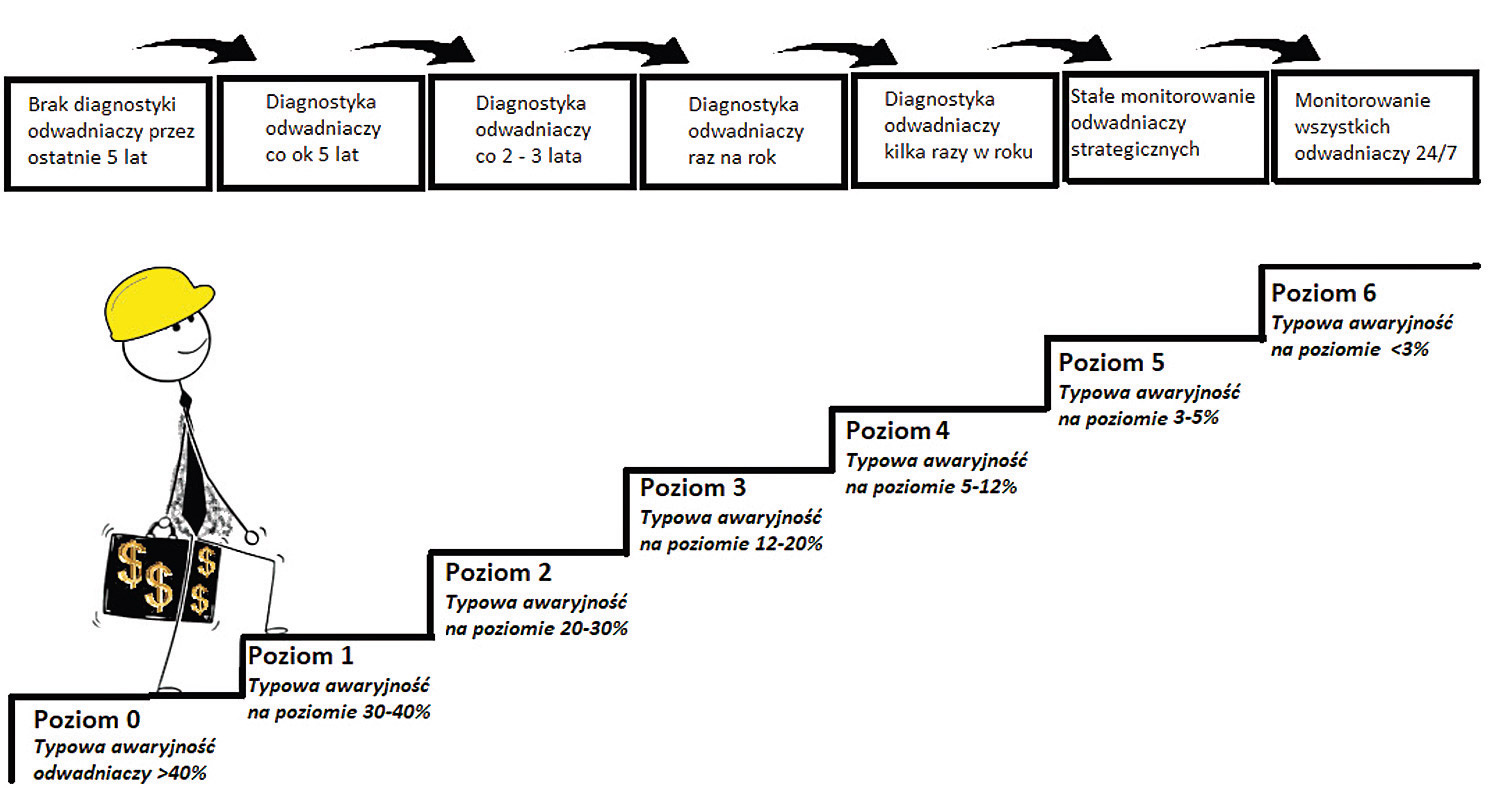
Rysunek 3. Wpływ częstotliwości diagnostyki odwadniaczy na poziom awaryjności
Zakłady parowe, w których praktyka regularnej diagnostyki odwadniaczy nie istnieje narażone są na ok. 40% uszkodzonych odwadniaczy. To całkiem sporo prawda? Zakładając, że odwadniacz może przepuścić powiedzmy 500 kg/h kondensatu i popsuje się w pozycji otwartej, straty w skali doby/tygodnia/miesiąca/roku będą ogromne. Ale straty finansowe to jedno. Przepuszczające odwadniacze to również większe ciśnienie kondensatu, więc do rachunku należy dopisać spadek wydajności prawidłowo działających odwadniaczy znajdujących się w jego pobliżu i negatywny skutek środowiskowy. A co gdy wadliwy odwadniacz jest zablokowany? Wówczas brak jego pracy powoduje zawodnienie instalacji parowej, uderzenia wodne, korozję rurociągów, erozję zaworów, problem z uzyskaniem prawidłowej temperatury procesowej. Rysunek nr 4 przedstawia zebrane negatywne czynniki wadliwie pracujących odwadniaczy.
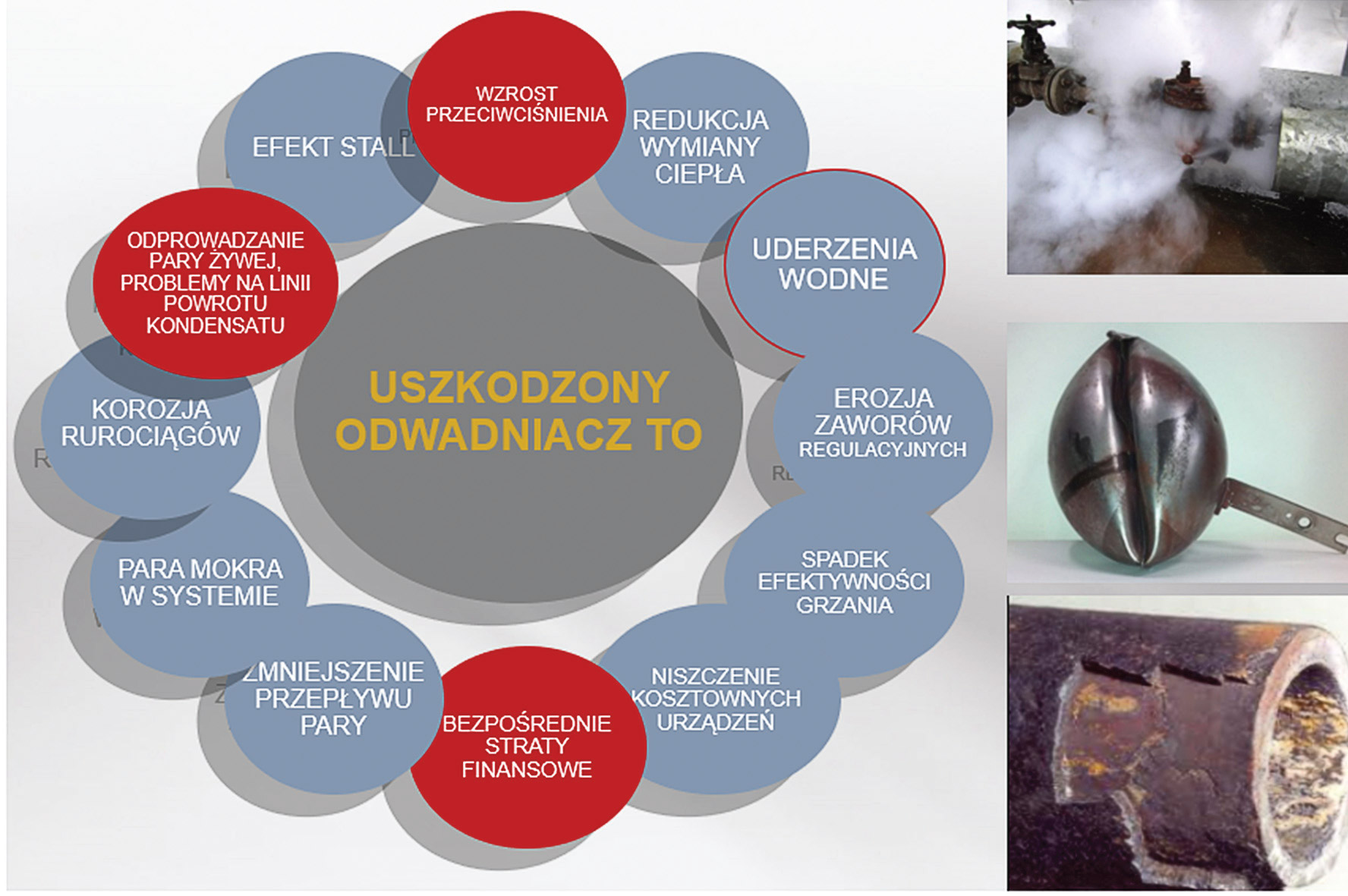
Rysunek 4. Skutki wadliwie działających odwadniaczy
Koszt zwrotu inwestycji w postaci uzupełniania izolacji na armaturze jest niesłychanie szybki i oscyluje przeważnie w granicach 6-11 miesięcy.
JAK DIAGNOZOWAĆ ODWADNIACZE?
Załóżmy, że decydujemy się na wariant pierwszy, czyli zlecamy diagnostykę odwadniaczy firmie zewnętrznej. Czego powinniśmy się spodziewać po diagnostyce? Przede wszystkim dowiedzmy się jakimi narzędziami dysponuje diagnosta. Do prawidłowej oceny odwadniaczy potrzeba odpowiedniego pomiaru temperatury i analizy ultradźwięków. Większość testerów powinna być kalibrowana raz na rok, by diagnostyka odbyła się w sposób poprawny. Osoba przeprowadzająca pomiar powinna ocenić, czy odwadniacz jest prawidłowo zamontowany, czy nadaje się do konkretnej aplikacji, czy przypadkiem nie powoduje zawodnienia urządzenia wymiany ciepła.
A co po badaniu? Oprócz zdiagnozowania w jakim stanie znajdują się nasze odwadniacze, czyli które działają poprawnie, które są zablokowane, a które przepuszczają parę, oczekujmy rzetelnej inwentaryzacji. Jest ona niezbędna do tego, aby obsługa podczas wymiany wiedziała jaki typ odwadniacza ma wymieniać, jakie ma on przyłącze, gdzie odwadniacz się znajduje i w jakim jest stanie. Dobrze jest wiedzieć jakie straty pary generuje, by zastosować hierarchię prac (począwszy od odwadniaczy generujących najwięcej strat energii). Warto określić również odpowiednią częstotliwość badania w zależności od procesów, bądź kampanii produkcyjnej.
Decydując się na wariant drugi, czyli regularne monitorowanie odwadniaczy we własnym zakresie niezbędne jest odpowiednie wykorzystanie dostępnych narzędzi. Tu zdecydowanie warto zwrócić uwagę na jeden z najbardziej zaawansowanych software’ów na świecie, tj. SAGE firmy Armstrong International. Dzięki niemu sami zinwentaryzujemy odwadniacze grupując je tak jak chcemy. Możemy wyodrębnić je wg wydziałów, linii produkcyjnych, czy ze względu na ich wykorzystanie.
To my decydujemy jak będzie wyglądać struktura odwadniaczy w oprogramowaniu. Po określeniu struktury i wpisaniu podstawowych danych możemy przejść do budowania bazy odwadniaczy. Wszystkie dane będą znajdowały się w „chmurze” co daje pewność, że nie ulegną one utraceniu. I tak, dla każdego odwadniacza wybieramy w aplikacji producenta, typ, model, rodzaj i wielkość przyłącza, ciśnienie robocze, możemy zrobić jego zdjęcie, opisać jakie ma zawory odcinające przed, za odwadniaczem i na by-passie, zaznaczyć, czy jest obecny filtr siatkowy, czy zawór zwrotny. Im więcej danych wprowadzimy tym większą liczbą danych będziemy mogli zarządzać.
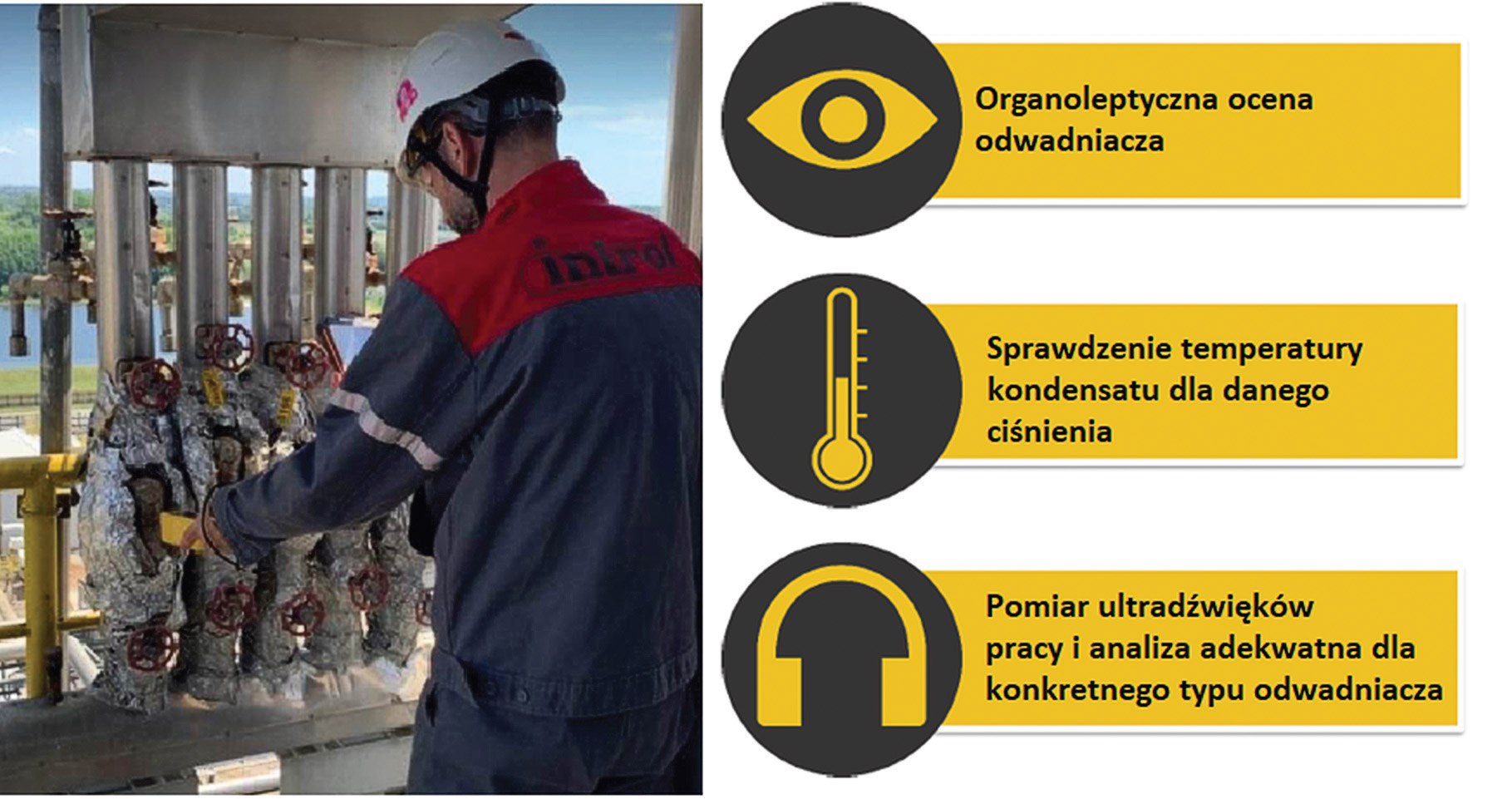
Rysunek 5. Etapy diagnostyki odwadniaczy
Aplikacja pozwala na sprawdzanie historii badania, tak więc możemy śledzić trendy pracy każdego z nich, mieć pod kontrolą stopień ich awaryjności, czy częstotliwość ich wymian. Dostęp do aplikacji możemy określić dla kilku osób i dedykować odpowiedzialność konkretnym pracownikom.
Dopełnieniem aplikacji SAGE jest tester SAGE UMT, który pracuje w oparciu o zebrane przez nas dane w aplikacji. Podczas diagnostyki wykorzystujemy aplikację SAGE w wersji mobilnej i tester parujemy za pomocą bluetooth’a z telefonem lub tabletem. Po wybraniu interesującego nas odwadniacza w aplikacji, tester dokonuje pomiaru temperatury i ultradźwięków.
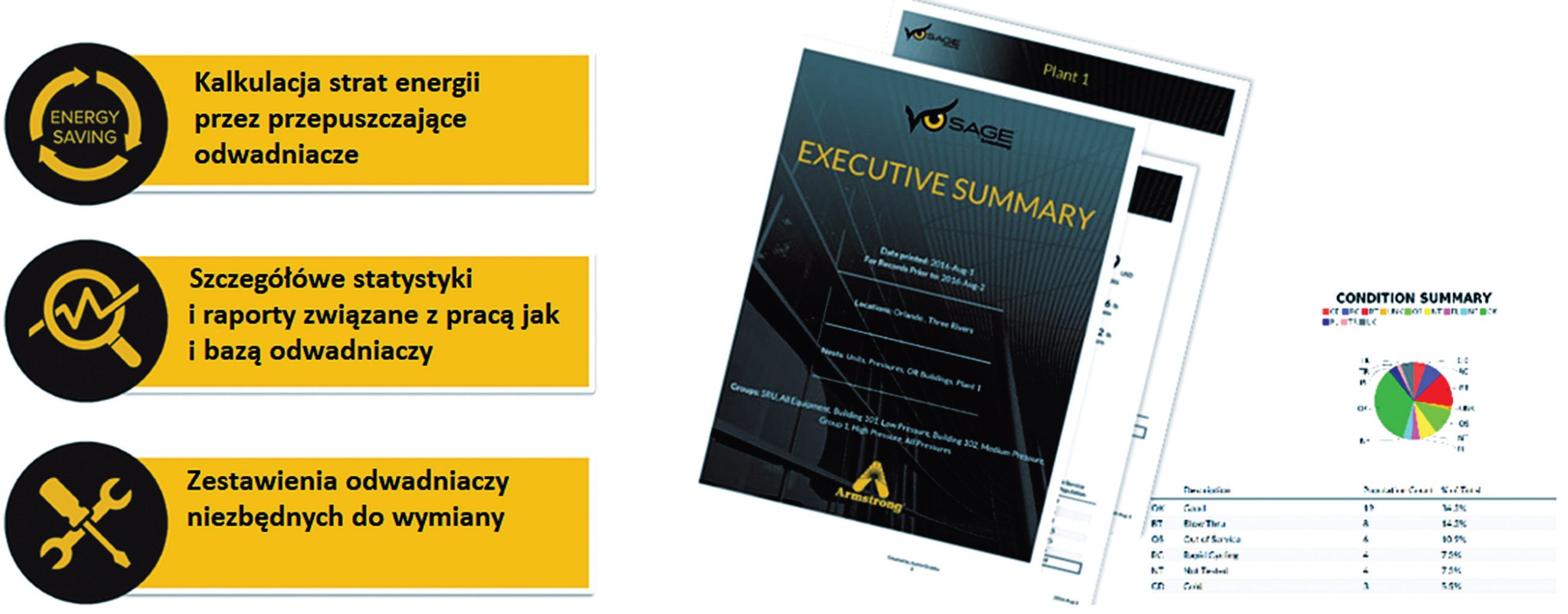
Rysunek 6. Raporty z badania odwadniaczy – elementy
Tester dokładnie wie jakich algorytmów ma się spodziewać dla prawidłowej pracy odwadniacza, a jakich dla odwadniacza przepuszczającego parę. Co najważniejsze, pomiary są powtarzalne i nie ma możliwości samodzielnej interpretacji wyniku. Tester nie wymaga również żadnej kalibracji, gdyż odbywa się ona poprzez aplikację.
Po przeprowadzeniu diagnostyki czas na analizę zebranych danych. Do tego służą raporty, które w każdej chwili możemy wygenerować z SAGE’a. Zawierają one listę wszystkich zinwentaryzowanych odwadniaczy, ich stan pracy, kalkulacje strat energii dla odwadniaczy przepuszczających parę, szczegółowe statystyki z istniejącego stanu, z podziałem na producentów, typy, czy z podziałem na miejsca ich zastosowania. Ponadto możemy wygenerować raport zestawiający wszystkie odwadniacze do wymiany i przekazać go bezpośrednio osobom odpowiedzialnym za serwis.
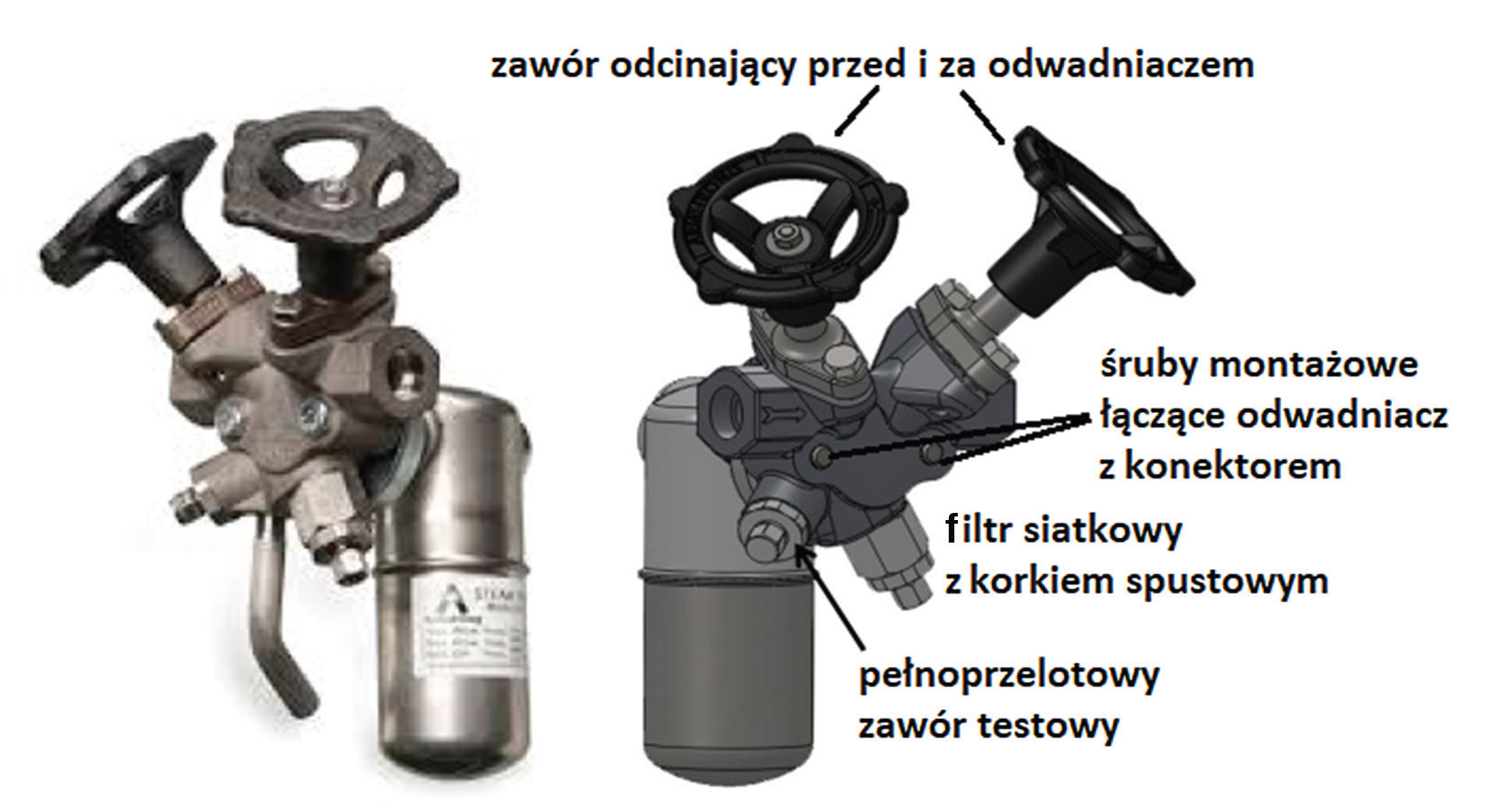
Rysunek 7. Stacja odwadniająca
W KWESTII WYMIANY ODWADNIACZY
Na koniec nie zapominajmy, że spore potencjalne oszczędności drzemią w kosztach wymiany odwadniaczy. Wszak prace serwisowe bywają horrendalnie duże z uwagi na odstawienie produkcji, czas operacyjny niezbędny na wymianę odwadniaczy, czy wystudzenie instalacji. Warto stosować takie odwadniacze, które maksymalnie skrócą czas niezbędny na wymianę. Rozwiązaniem są uniwersalne konektory, do których odwadniacze każdego typu montowane są za pomocą dwóch śrub, tworząc stacje odwadniające.
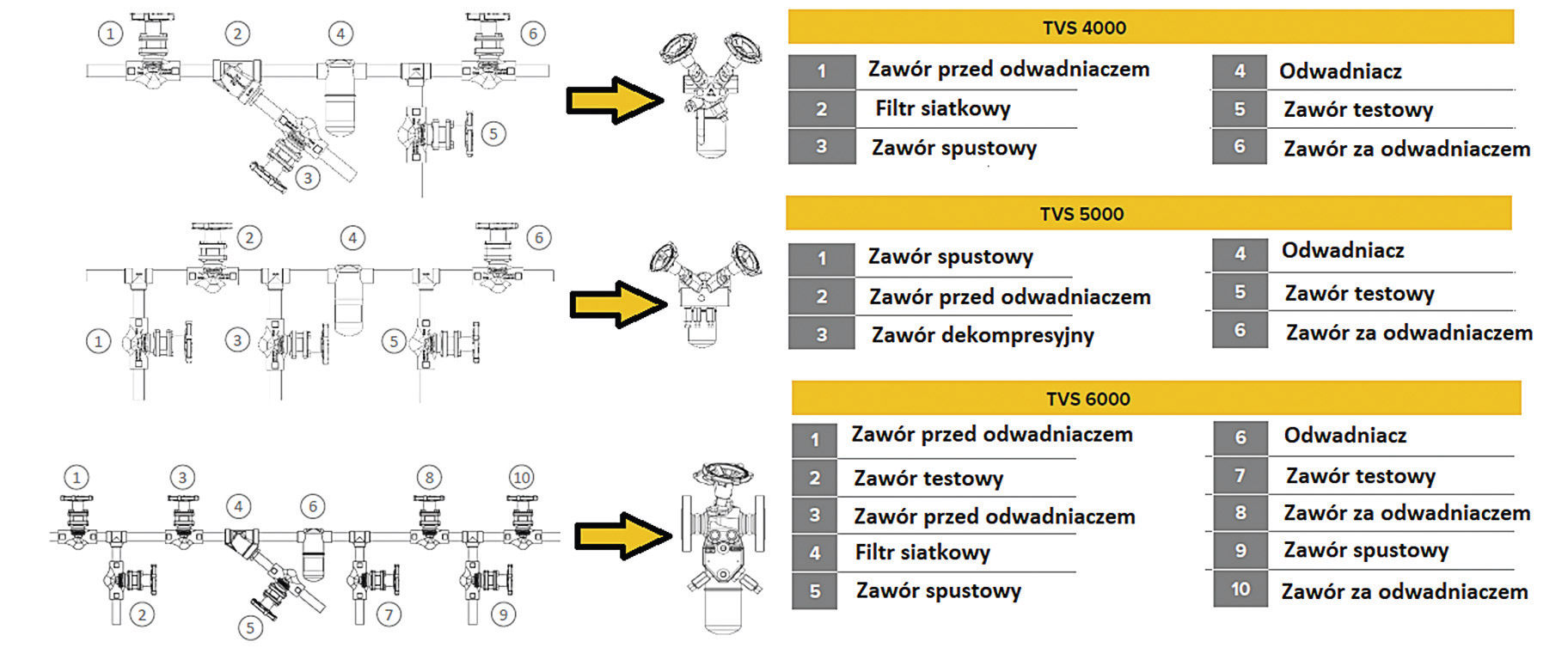
Rysunek 8. Komponenty stacji odwadniających
ZARZĄDZANIE ODWADNIACZAMI = REDUKCJA ZUŻYCIA CIEPŁA
Reasumując, skuteczne zarządzanie odwadniaczami, regularne ich testowanie i szybka wymiana uszkodzonych urządzeń to swoista autostrada w kierunku redukcji zużycia ciepła. O ile stwierdziliśmy, że termoizolacja zwraca się w kilka miesięcy, to biorąc pod uwagę dzisiejsze ceny energii, eliminowanie strat pary na odwadniaczach poprzez ich szybką wymianę zwraca się zazwyczaj w kilka – kilkanaście tygodni. Ponadto, odpowiednie zarządzanie odwadniaczami podniesie efektywność energetyczną wymiany ciepła i poprawi efektywność procesów zachodzących w zakładach wykorzystujących parę. Sprawi, że unikniemy problemów związanych z uderzaniami wodnymi, czy erozją zaworów odpowiedzialnych za regulację przepływu pary.
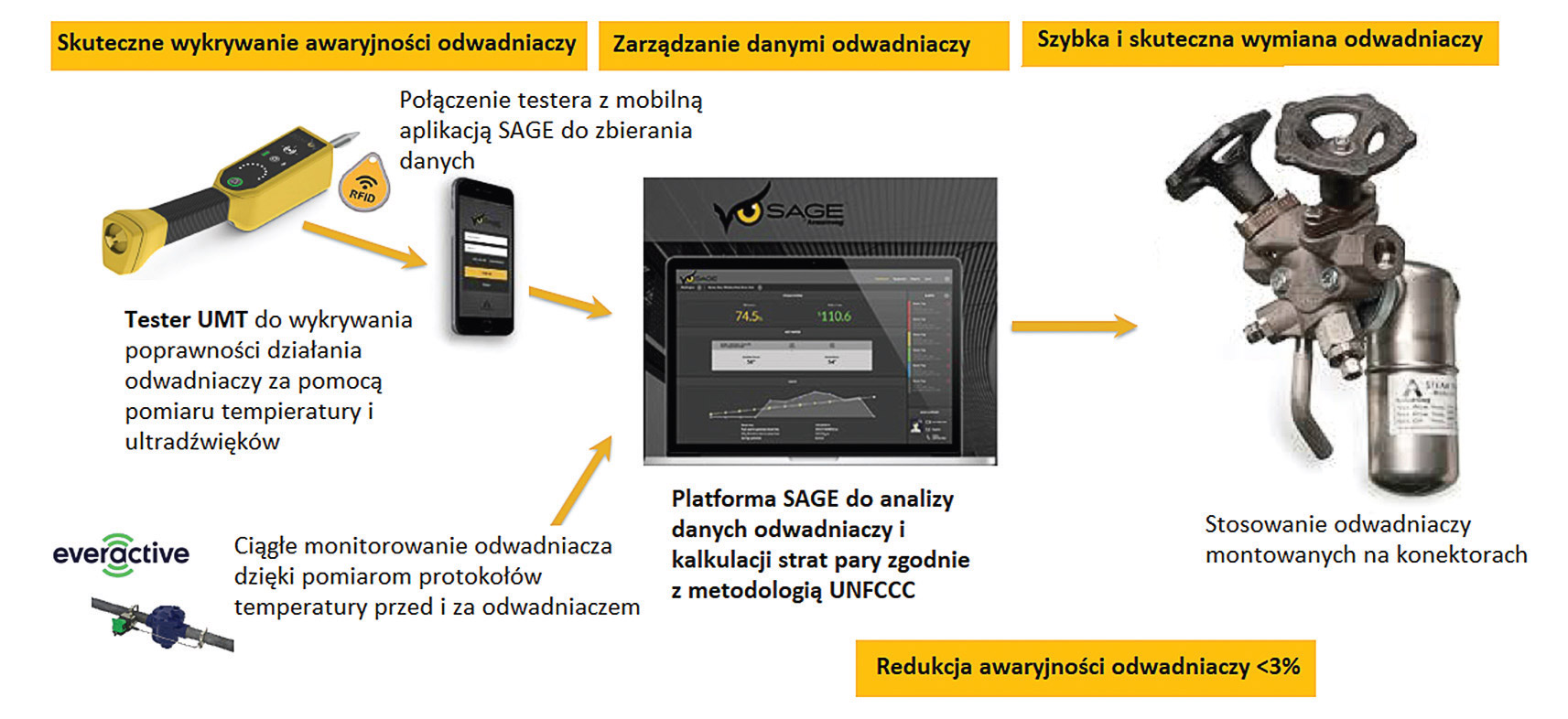
Rysunek 9. Trzy kroki do zarządzania odwadniaczami parowymi