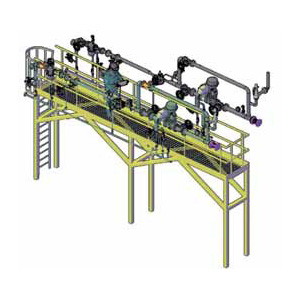
Granulowanie pasz można zdefiniować jako konwersję drobno zmielonego zacieru paszy na gęste granulki lub kapsułki, w procesie obejmującym bezpośredni wtrysk pary (wilgoć i ciepło) oraz ciśnienie mechaniczne. Kilka czynników ma wpływ na jakość granulatu. Przede wszystkim formuła paszowa (użyte surowce i dodatki).
Wcześniej wiadomo było, że skrobia i jej żelowanie są najważniejszym czynnikiem dla osiągnięcia pożądanej jakości granulatu. Ostatnie raporty wskazują jednak, że pozytywny wpływ białka na jakość granulatu jest znacznie ważniejszy niż wpływ skrobi. Włączenie oleju ma niekorzystny wpływ na jakość granulatu. Jest to przypisywane efektowi powlekania olejem cząstek zacieru, które zapobiegają ich penetracji przez parę. Olej zmniejsza tarcie generowane między matrycą a cząstkami zasilającymi, a następnie zmniejsza szybkość żelatynizacji skrobi. W celu optymalizacji procesu warto rozważyć modernizację układu dostarczania pary wodnej do granulatora.
WPŁYW PARY NA JAKOŚĆ GRANULATU
Gdy pasza przechodzi przez kondycjoner, narażona jest na działanie pary pod wysokim ciśnieniem. Para ta dostarcza ciepło i wilgoć, które są wymagane do żelowania skrobi, adhezji cząstek, częściowego trawienia paszy i uszkodzenia patogenów paszowych. Temperatura pary i czas, w którym pasza zacierowa pozostaje w kondycjonerze, mają duży wpływ na trwałość produkowanego granulatu. Kondycjonowanie paszy w temperaturze 80°C jest wystarczające, aby wytworzyć granulki o odpowiedniej jakości. Minimalny czas, jaki pasza powinna pozostać w kondycjonerze, aby wytworzyć trwały granulat, to 30 sekund. Kondycjonery o wydłużonym czasie pracy, w których pasza może pozostawać w kondycjonerze przez około 3-4 minuty, mogą być użyte do poprawy lepkości granulatu.
Proces kondycjonowania jest najważniejszą częścią każdego systemu granulowania pasz i zależy od:
- wilgotności,
- ilości jakości pary wodnej,
- blendowania,
- czasu retencji.
Powody stosowania pary wodnej w procesie kondycjonowania:
- smarowanie w celu zwiększenia tempa produkcji,
- smarowanie w celu wydłużenia żywotności matrycy,
- smarowanie w celu redukcji kosztów energii spowodowanych przez tarcie,
- do żelowania skrobi w celu uzyskania odpowiednich wartości odżywczych.
ARMSTRONG STEAM HARNESS
Armstrong Steam Harness (ASH) to kompleksowy, w pełni zintegrowany pakiet systemowy, który łączy niezawodne i trwałe produkty firmy Armstrong z nowoczesną technologią. Powstał po to, aby dostarczać parę wodną o niezmiennej, wysokiej jakości, w celu uzyskania ciągłego i powtarzalnego poziomu wydajności oraz sprawności. Armstrong Steam Harness jest zawsze dostosowany do indywidualnych wymagań i posiadanych urządzeń, przynosząc wymierne oszczędności energii i podnosząc wydajność procesu. Korzystając z holistycznego systemu, nasi eksperci biorą pod uwagę cały zakład, projektując układ z uwzględnieniem czynników takich jak poprawne umieszczenie urządzeń z zachowaniem ergonomii i bezpieczeństwa dla operatorów.
ASH został stworzony aby rozwiązywać problemy oraz im zapobiegać poprzez działania tj.:
- redukcja ilości korków parowych, które powodują „zalepianie” granulatora oraz nieplanowane postoje w produkcji,
- zapewnienie właściwego odprowadzania kondensatu i dostarczanie suchej, mierzalnej, wysokiej jakości pary do granulatora lub ekstrudera,
- grupowanie kosztów energii i sprawności wg poszczególnych formuł (w niektórych przypadkach korelują z parametrami granulowania/wytłaczania),
- podnoszenie bezpieczeństwa i obniżanie strat energii poprzez stosowanie odpowiednich pokrowców izolacyjnych wielorazowego użytku.
ZASADA DZIAŁANIA
1. Para wodna zasila ASH.
2. Ręczna przepustnica na wlocie zapewnia całkowitą izolację w przypadku potrzeby odcięcia zasilania.
3. Czujnik urządzenia do monitoringu jakości pary Armstrong Steam QM®-1 można w razie potrzeby przenieść do dostępnego króćca, aby zmierzyć jakość pary na zasilaniu ASH.
4. Kieszeń odwadniająca wychwytuje kondensat i zanieczyszczenia z instalacji dystrybucji pary wodnej; odwadniacz dzwonowy Armstrong TVS odprowadza kondensat z kieszeni odwadniającej; wysokociśnieniowy zawór umożliwia ręczne usuwanie zanieczyszczeń wychwyconych przez nóżkę kroplową. (A)
5. Separator cyklonowy usuwa z pary wilgoć i cząstki większe niż 10 mikronów; odwadniacz dzwonowy Armstrong TVS odprowadza kondensat z separatora do instalacji powrotnej kondensatu pod wysokim ciśnieniem. (B)
6. Manometr i przetwornik ciśnienia zainstalowane przed separatorem dostarczają informacje odnośnie ciśnienia pary wlotowej i przekazują sygnał do PLC/HMI.
7. Para przepływa przez filtr siatkowy typu Y, który wychwytuje cząstki większe niż 0,0055 ”; zawór umożliwia ręczne usuwanie cząstek; zanieczyszczenia zostają odprowadzone do atmosfery. (C)
8. VERIS Accelabar® mierzy przepływ pary i kompensuje zmiany ciśnienia pary, sygnał przekazywany do panelu operatorskiego granulatora lub ekstrudera. (D)
9. Armstrong Steam QM®-1 mierzy jakość pary; informacje przesyłane przez Modbus do PLC/HMI dostarczanego przez Armstrong. (E)
10. Zawór redukcyjny Armstrong obniża ciśnienie pary. (F)
11. Zawór bezpieczeństwa.
12. Manometr i przetwornik ciśnienia zainstalowane za zaworem redukcyjnym dostarczają informacje odnośnie ciśnienia pary zredukowanej i przekazują sygnał do PLC/HMI. (G)
13. Kieszeń odwadniająca zbiera i odprowadza kondensat pomiędzy zaworem redukcyjnym, a automatycznym zaworem kulowym z pełnym portem; kondensat odprowadzony jest do powrotu kondensatu o niskim ciśnieniu; odwadniacz termostatyczny usuwa schłodzony kondensat, powietrze i gazy niekondensujące się (NCG), odprowadzenie są do atmosfery. (H)
14. Zawór kulowy kołnierzowy z pełnym portem i napędem elektropneumatycznym jest sterowany przez panel operatorski granulatora lub ekstrudera; mechaniczne przełączniki potwierdzają całkowite otwarcie zaworu panelu operatorskiego granulatora lub ekstrudera. To wyposażenie nie jest standardowe, ale może być dostępne jako opcja. (I)
15. Panel operatorski granulatora lub ekstrudera przesyła sygnał do pozycjonera typu SMART umieszczonego na zaworze regulacyjnym, który doprowadza parę do komory kondycjonera; pozycjoner cyfrowy wysyła sygnał zwrotny do systemu kontroli granulatora lub ekstrudera, potwierdzając procent otwarcia zaworu sterującego; cała para jest wtryskiwana bezpośrednio do komory. Zawór jest wykonany w klasie szczelności VI, przez co może być również używany jako zawór on/off . (J)
16. Wizualny manometr i przetwornik temperatury zainstalowane za zaworem regulacyjnym monitorują dopływ temperatury pary do granulatora lub ekstrudera i przekazują informacje do panelu.
17. Elastyczne złącze wykonane z falistego węża ze stali nierdzewnej i pojedynczego oplotu ze stali nierdzewnej pochłania wibracje z komory kondycjonera. (K)
18. Szafka elektryczna z PLC i HMI dostarczana przez Armstrong. (L)

Rysunek 1 Przykładowy schemat systemu ASH
MONITORING I POMIARY
Dostęp do kluczowych danych w czasie rzeczywistym:
- ciśnienie pary na dolocie do ASH,
- jakość pary,
- jakość pary (średnia) na tonę paszy,
- ilość wody dodanej poprzez parę na tonę produktu,
- zużycie pary na godzinę,
- zużycie pary na tonę paszy,
- skumulowane zużycie pary [kg],
- pobór energii cieplnej [kW],
- energia cieplna na tonę produktu [kW/h],
- koszt pary na godzinę [PLN],
- koszt pary za tonę pasz [PLN],
- natężenie silnika na tonę produktu [amp / tonę produktu],
- natężenie silnika w odniesieniu do przepływu pary,
- pomiar zredukowanego ciśnienia pary do kondycjonowania produktu,
- dostosowanie ASH według poszczególnej formuły (informacje wymagane od producenta granulatora via Ethernet).

Rysunek 2. System ASH
SERWIS I WSPARCIE — PRZED, W TRAKCIE I PO INSTALACJI
Każda instalacja mediów w otoczeniu granulatora lub ekstrudera, czy to nowa, czy istniejąca, ma unikalną konfigurację rurociągów oraz połączeń mechanicznych, więc dobór rozpoczyna się od oceny faktycznego stanu instalacji. Powinno zmierzyć się fizyczną przestrzeń, zidentyfi kować ograniczenia i określić specyficzne potrzeby obiektów otaczających granulator lub ekstruder przed dostosowaniem ASH do istniejącej infrastruktury.
OCENA TERMICZNA POMAGA ZAPEWNIĆ WYDAJNOŚĆ ASH
Posiadanie poprawnie pracującego systemu pary i kondensatu ma zasadnicze znaczenie dla wydajności ASH. Ocena infrastruktury cieplnej w zakładzie, pozwala lepiej przygotować się do poprawy instalacji dystrybucji pary oraz maksymalizacji jakości i ilości pary dostarczanej do kondycjonera i/lub komory kondycjonowania.
OD AUDYTU NA MIEJSCU, DO INSTALACJI „POD KLUCZ”
Specjalista od inżynierii termicznej jest obecny na każdym etapie realizacji inwestycji/modernizacji, tj. przed, w trakcie i po instalacji układu ASH, aby upewnić się, że proces uruchomienia i rozruchu jest płynny, a obsługa układu jest wygodna dla personelu. Konsekwentnie koncentrujemy się na bezpieczeństwie operatorów, ergonomii i zapewnieniu, że granulator lub ekstruder utrzymują optymalną jakość i ilość pary.