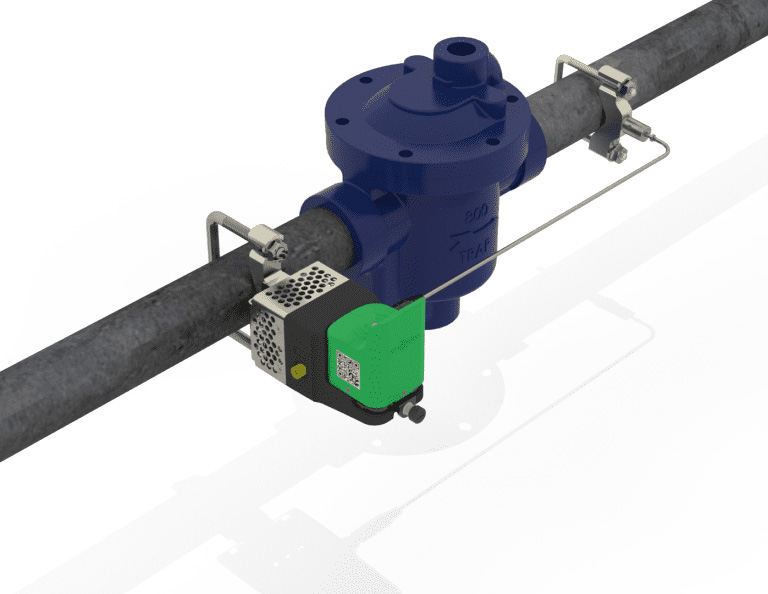
Świat zmienia się na naszych oczach. To zdanie rozbrzmiewa bardzo często we wszelakich mediach i jest niezmiernie istotne. Walka ze zmianami klimatycznymi, a może bardziej jej zapowiedzi, nabierają rozpędu, a świat zmierza bezsprzecznie ku dekarbonizacji. W listopadzie 2019 roku Parlament Europejski przyjął rezolucję wzywającą do neutralności klimatycznej do 2050 roku oraz za cel postawił ograniczenie emisji do 55% do 2030 roku. Światowi liderzy w branży spożywczej, kosmetycznej, czy farmaceutycznej zapowiedzieli już wdrażanie zmian w swoich fabrykach. To dobry znak dający impuls całej branży, że najwyższy czas na zmiany.
Zakłady produkcyjne potrzebują stworzyć mapy drogowe określające etapy systematycznych zmian zmierzających ku dekarbonizacji. Należy przy tym pamiętać, że to, co jest dobre dla jednego zakładu produkcyjnego, niekoniecznie znajdzie zastosowanie w innym. Z całą pewnością jednak wszyscy producenci muszą systematycznie zwiększać efektywność energetyczną. Rozważmy zatem krok po kroku, co należy zrobić, by sukcesywnie poprawiać efektywność i zmniejszać emisyjność CO₂. Analizę opieramy głównie na branży spożywczej, w której powszechnie wykorzystywana jest para wodna.
KROK 1:
ZWIĘKSZAMY EFEKTYWNOŚĆ ENERGETYCZNĄ INSTALACJI POPRZEZ ZARZĄDZANIE ODWADNIACZAMI
W zakładach produkcyjnych wykorzystujących parę wodną konieczna jest odpowiednia polityka zarządzania odwadniaczami. Do tego zadania stworzony jest najbardziej zaawansowany software na świecie, tj. SAGE firmy Armstrong.
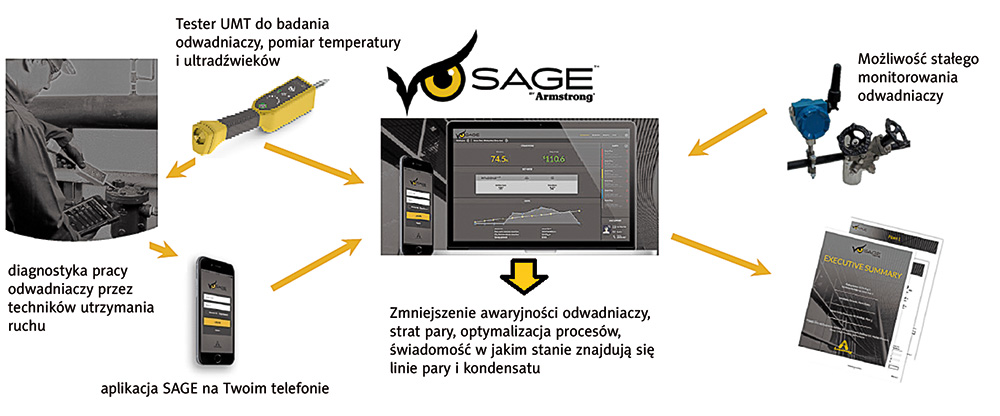
Rysunek 1. System SAGE
Dzięki niemu możemy stale monitorować i zarządzać odwadniaczami oraz linią powrotu kondensatu. Stosując go pozyskamy miarodajne dane o stanie odwadniaczy i zinwentaryzujemy je grupując na poszczególne wydziały, sekcje. Wygenerujemy także raporty o stanie faktycznym odwadniaczy na każde nasze żądanie. Ponadto, w miejscach najbardziej krytycznych dla zakładu, możemy zastosować urządzenia stale monitorujące pracę odwadniaczy i zintegrować je właśnie z softwarem SAGE.
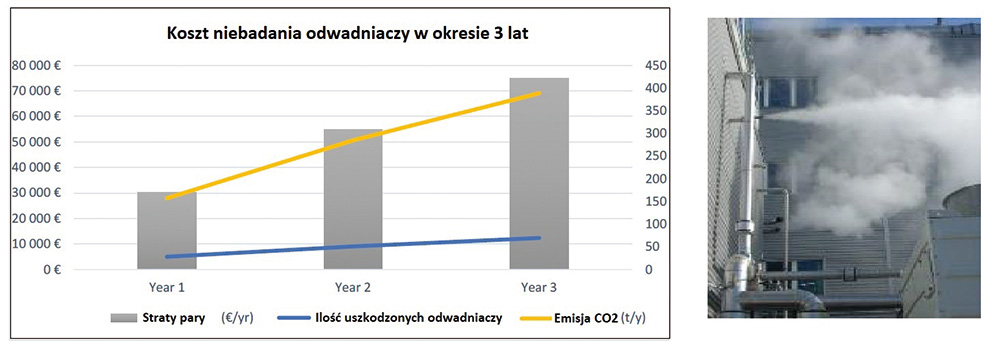
Rysunek 2. Przykład analizy kosztów
Jeśli mamy jednak wątpliwości, czy aby na pewno warto odpowiednio zarządzać odwadniaczami, bardzo istotna jest świadomość ile kosztuje nicnierobienie. Na następnej stronie przedstawiam wykres obrazujący jak rosną straty pary w okresie trzech lat braku kontroli pracy odwadniaczy. Rysunek 2 przedstawia również wzrost emisji CO₂ w kontekście dekarbonizacji. Przyjmując, że zakład w ogóle nie przeprowadza diagnostyki odwadniaczy, ich awaryjność w każdym momencie wynosi zazwyczaj powyżej 40%.
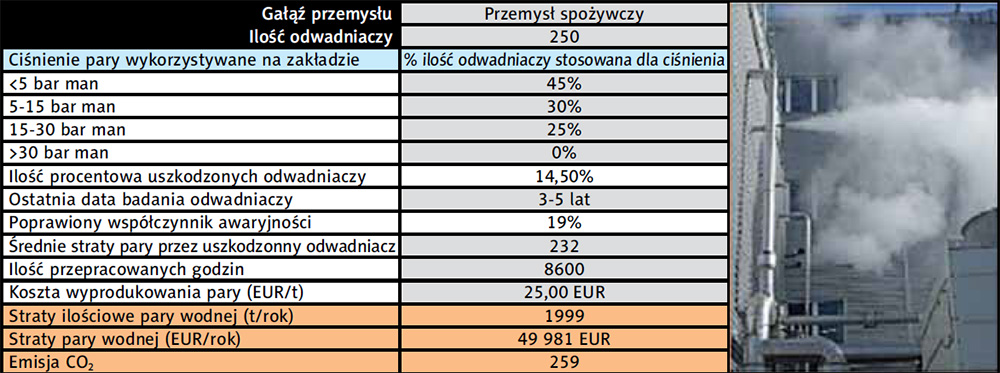
Rysunek 3. Przykład analizy kosztów
Uszkodzone odwadniacze to nic innego jak straty pary żywej, tj. energii i zwiększenie emisji CO₂ oraz przeciwciśnienia. Z kolei, gdy odwadniacze są zablokowane sprawiają, że para jest z dużą zawartością kondensatu, a to oznacza problemy w cały systemie parowym. W rezultacie mamy erozję zaworów regulacyjnych, korozję rurociągów, czy uderzenia wodne. Co więcej – zablokowane odwadniacze redukują wymianę ciepła.
Zacznijmy od regularnego przeprowadzania badania odwadniaczy celem zmniejszenia ich stopnia awaryjności do ok. 12–20%.
Jaką zatem przyjąć metodologię w działaniu? Zacznijmy od regularnego przeprowadzania badania odwadniaczy celem zmniejszenia ich stopnia awaryjności do ok. 12 … 20%. Bardzo istotny jest odpowiedni wybór technologii odwadniaczy adekwatny do procesu. W miejscach kluczowych dla produkcji można dodatkowo stale monitorować pracę odwadniaczy, dzięki zastosowaniu urządzeń dedykowanych do ich monitorowania.
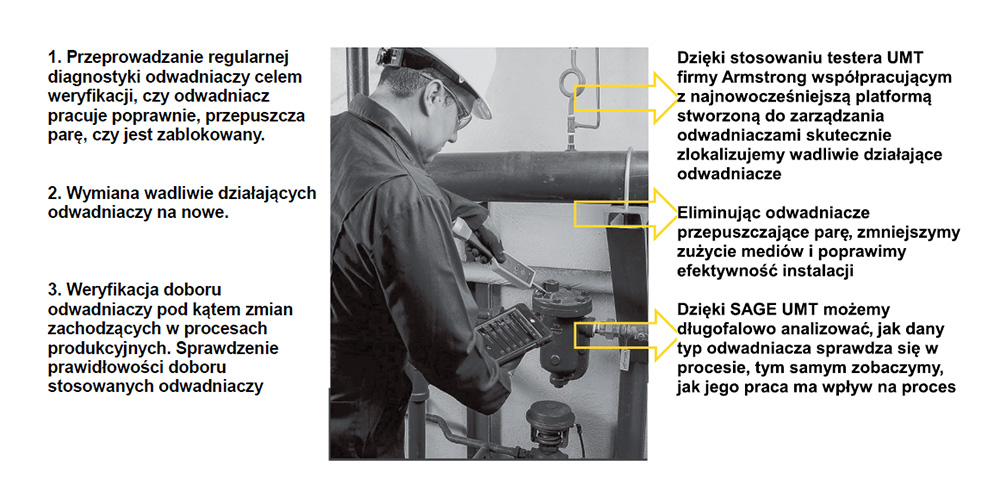
Rysunek 4. Trzy kroki prawidłowej kontroli odwadniaczy
Najnowszym tego typu rozwiązaniem jest system Everactive, czyli urządzenie bezprzewodowe i bezobsługowe, łatwe w instalacji i kompatybilne ze wszystkimi markami i modelami odwadniaczy. Stosując Everactive można otrzymywać alerty o awariach odwadniaczy w momencie ich wystąpienia. Umożliwia to ich naprawę lub wymianę uszkodzonych odwadniaczy, zanim spowodują one poważne problemy w systemie parowym. Jest to przełomowa technologia oferująca maksymalną wydajność i niezawodność, przy jednoczesnym zminimalizowaniu ingerencji w istniejącą infrastrukturę IT.
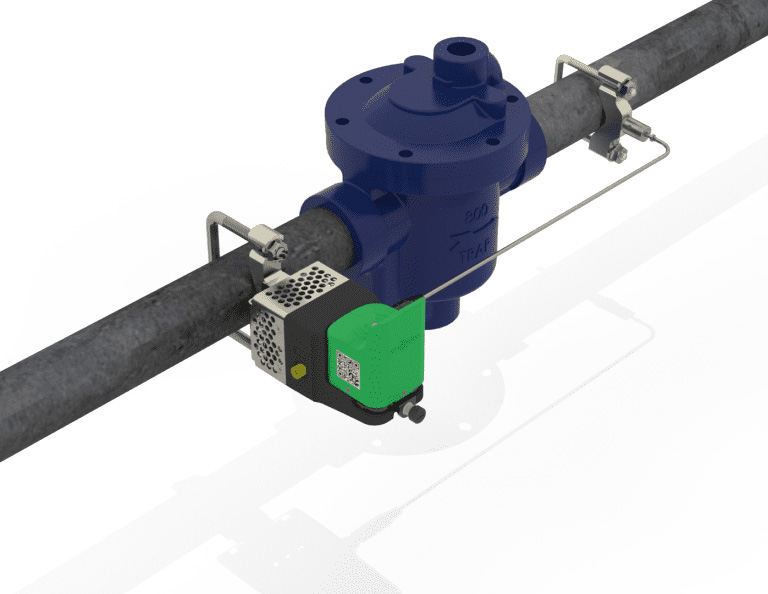
Rysunek 5. Everactive
KROK 2:
STOSOWANIE URZĄDZEŃ LEPSZEJ JAKOŚCI
Stosowanie urządzeń mniej awaryjnych, o większej żywotności stanowi kolejny aspekt, który warto wziąć pod uwagę. Odnosząc się do zarządzania odwadniaczami, z pomocą SAGE możemy analizować również zawory odcinające przed i za odwadniaczem, filtry, czy zawory spustowe. Dokonując wymian uszkodzonych elementów, warto jest stosować urządzenia kompaktowe w postaci stacji odwadniających.
Rysunek 6. Zestawienie elementów wchodzących w skład stacji odwadniającej Armstrong TVS 6000UD
Zajmują one zdecydowanie mniej miejsca, dzięki czemu eliminowana jest znaczna ilość uszczelnień i potencjalnych wycieków. Co oczywiste, to również ma znaczący wpływ w kontekście zwiększania efektywności.
KROK 3:
IZOLOWANIE ZAWORÓW
Płaszcze izolacyjne są znane nie od dziś, choć często błędnie pomijane. Stosowanie izolacji na zaworach, oprócz redukcji strat cieplnych wynikających z wymiany ciepła, zdecydowanie poprawią komfort pracy obsługi. Płaszcze izolacyjne dobrej jakości są odporne na warunki atmosferyczne i substancje chemiczne, łatwe w instalacji, demontażu i ponownej instalacji, umożliwiając szybki dostęp i łatwą obsługę urządzeń. Kluczową korzyścią jest możliwość wielokrotnego wykorzystania. Płaszcze izolacyjne są dostępne dla szeroko pojętej gałęzi zaworów, takich jak zasuwy, zawory grzybkowe, kulowe, przepustnice, zawory regulacyjne, zawory międzykołnierzowe. Mogą być stosowane również na kołnierzach, pompach, oprzyrządowaniach, głowicach i wszystkich skomplikowanych powierzchniach.
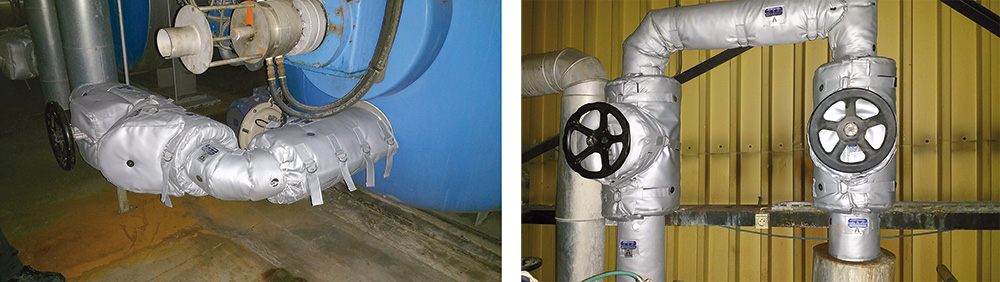
Rysunek 7. Stosowanie płaszczy izolacyjnych zmniejsza straty ciepła
Zarządzając mediami i energią w zakładzie stoimy przed wyzwaniem, jak dokonać oszczędności energetycznych i zmniejszać emisję CO₂ bez wpływu na proces produkcyjny.
KROK 4:
AUDYTY EFEKTYWNOŚCI ENERGETYCZNEJ, CZYLI POSZUKIWANIE OPTYMALIZACJI PROCESU
Zarządzając mediami i energią w zakładzie stoimy przed wyzwaniem, jak dokonać oszczędności energetycznych i zmniejszać emisję CO₂ bez wpływu na proces produkcyjny. W tym celu przeprowadza się audyty efektywności energetycznych. Zazwyczaj tego typu audyt ma nam dać wiedzę, jaki projekt możemy zaimplementować w naszym zakładzie, by powyższym wyzwaniom sprostać. Oczywiście, głównym faktorem jest czas zwrotu inwestycji. Zdecydowanie łatwiej podjąć decyzję inwestycji, gdy ten czas nie przekracza 2 – 3 lat. W oparciu o doświadczenie inżynierów firmy Armstrong, od lat zajmujących się audytami energetycznymi, została stworzona grafika uwzględniająca czas zwrotu inwestycji w latach, w skali procentowej możliwych oszczędności w wytwarzaniu pary wodnej.
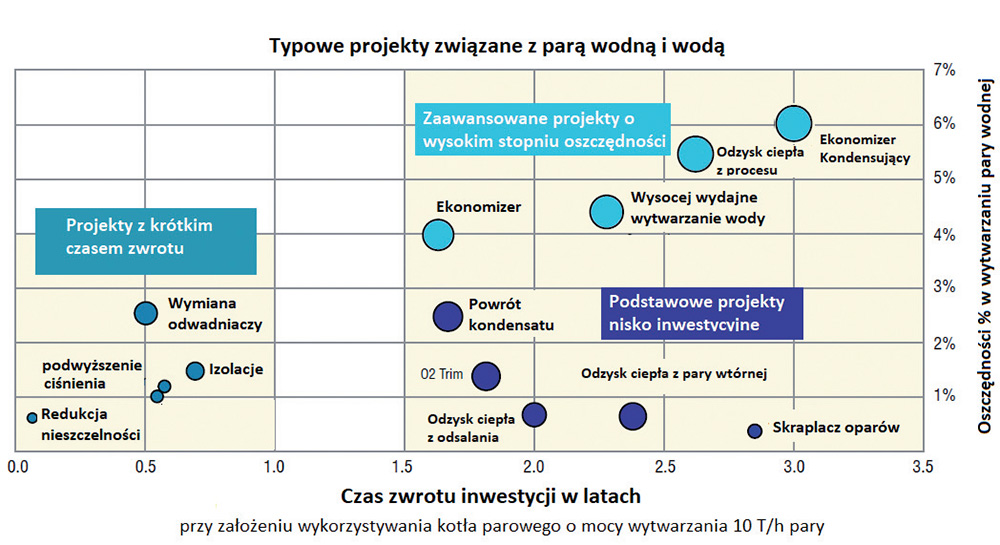
Rysunek 8. Macierz zwrotu z inwestycji
Analizując tę macierz, opisywane dotychczas przez nas kroki mieszczą się w projektach, w których czas zwrotu powinien zamknąć się w okresie 12 miesięcy. Skoro tak, decyzja o ich zaimplementowaniu jest stosunkowo łatwa.
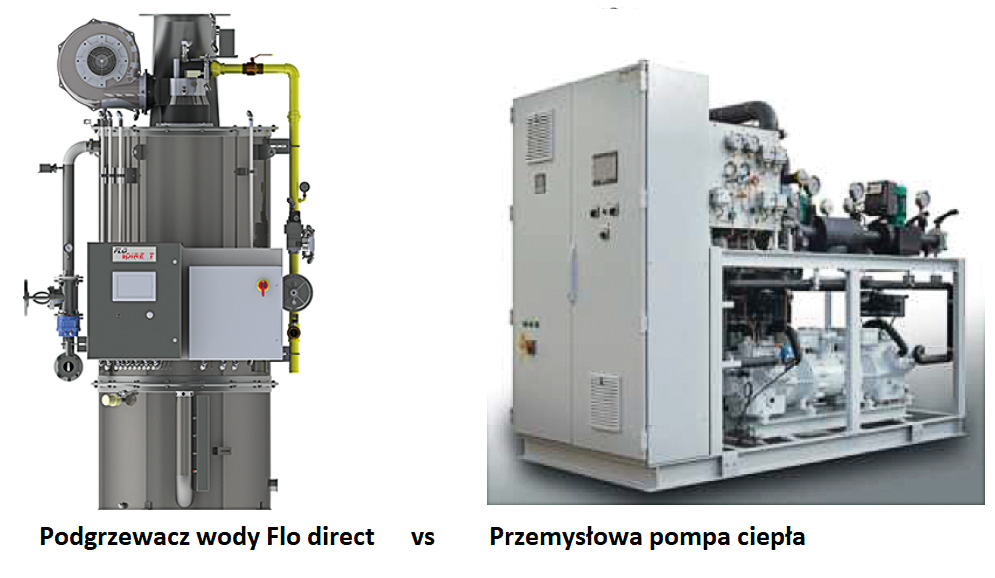
Rysunek 9. Alternatywne źródła ciepłej wody zmniejszą zastosowanie kotłów parowych
Z kolei te bardziej zaawansowane, wymagające dłuższego czasu oczekiwania na zwrot kosztów, tak na dobrą sprawę powinny już być stosowane w większości zakładów. Rzadko się spotyka zakład produkcyjny, który nie wykorzystuje powtórnie kondensatu, czy nie odzyskuje pary wtórnej przy wykorzystaniu rozprężacza. Najwięcej energii możemy odzyskać stosując ekonomizery na kotłach i wykorzystywać ciepło spalin np. do podgrzewu wstępnego wody.
KROK 5:
ODCHODZENIE OD PARY WODNEJ
Wracając do naszego głównego celu jaki chcemy osiągnąć, a mianowicie do dekarbonizacji, istnieje duże prawdopodobieństwo, że to przemysłowe pompy ciepła oraz wysoce efektywne podgrzewacze wody zrewolucjonizują proces pozyskiwania gorącej wody. Doprowadzą one do zmniejszenia zastosowania kotłów parowych w miejscach, w których para wodna nie będzie konieczna do procesu produkcyjnego. Wszak obecne układy grzania gorącej wody wykorzystujące kotły parowe generują straty na poziomie 20 … 30%. Stosując podgrzewacze Flo-direct wykorzystujące gaz do podgrzewania wody osiągniemy blisko 99,7% efektywność wymiany ciepła. Z kolei pompy ciepła wykorzystujące energię elektryczną do swojej pracy mogą podgrzewać wodę do 120°C. Ponadto mogą być zasilane energię geotermalną, pobierając ciepło z gruntu za pomocą sond geotermalnych, kolektorów itp. do celów grzewczych. Zaletą takiego rozwiązania jest stosunkowo stała dostępność energii przez cały rok. Pompy ciepła wykorzystujące studnie, rzeki, jeziora itp. jako źródło wody czerpią energię z systemów wymienników ciepła specjalnie zaprojektowanych do indywidualnych wymagań i warunków.
Woda dostępna w dużych ilościach jest wydajnym źródłem ciepła, zwłaszcza, że najczęściej posiada ona wysoką temperaturę. Brzmi EKO, prawda? O zasadności wyboru rozwiązania podgrzewania gorącej wody zdecyduje zapewne ekonomia i stosunek ceny energii elektrycznej do gazu i możliwości wykorzystywania naturalnych zasobów.
INNEJ DROGI NIE MA
Nie ma już odwrotu ze ścieżki dekarbonizacji. Na tej drodze niezbędna jest optymalizacja całej sieci cieplnej. Zakłady produkcyjne wykorzystujące temperaturę powyżej 110°C powinny skupić się maksymalnie na:
- unowocześnieniu kotłów stosując ekonomizery czy skraplacze oparów;
- maksymalizacji ilości odzyskiwanego kondensatu;
- wprowadzeniu systemu zarządzania kondensatem poprzez monitorowanie odwadniaczy parowych;
- izolowaniu zaworów;
- odzyskiwaniu ciepła z pary wtórnej.
Fabryki wykorzystujące w procesach ciepło poniżej 110°C powinny natomiast zminimalizować zapotrzebowanie na ciepło, poprzez zarządzanie procesem, a także przekształcić sieci parowe na sieci gorącej wody, celem osiągnięcia blisko 100% sprawności.