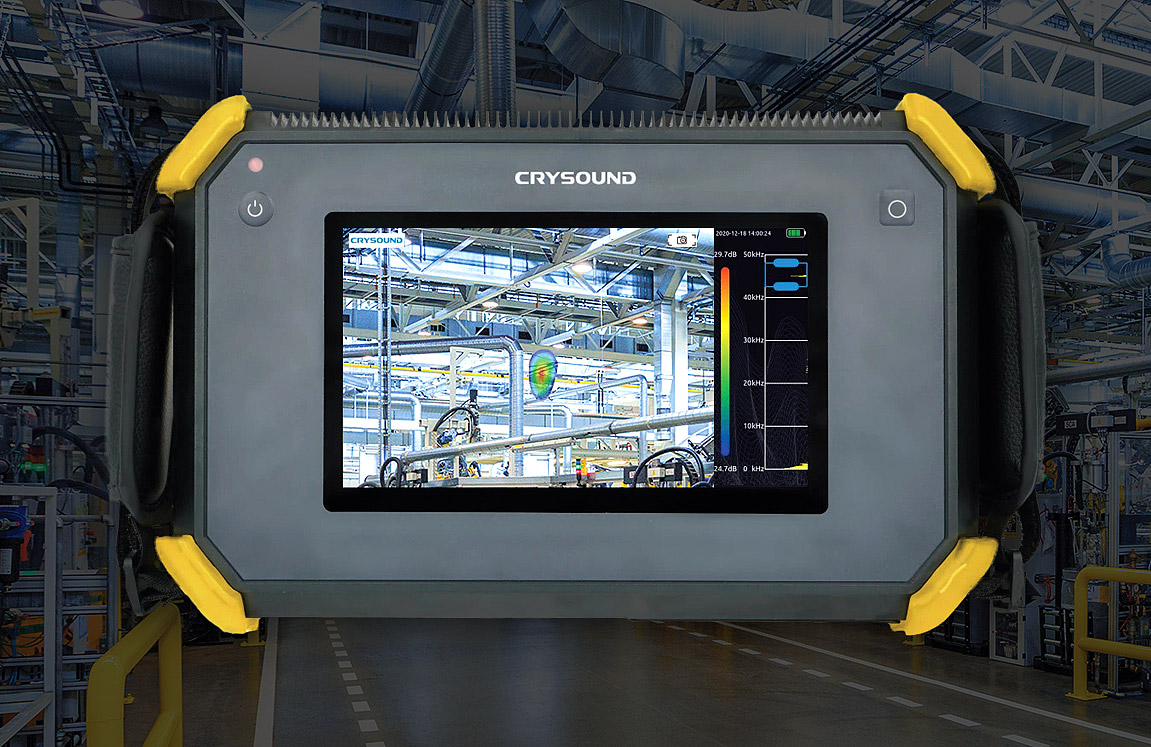
Rosnące koszty energii niepokoją zarówno osoby zarządzające budżetem domowym, jak i właścicieli, zarządy i dyrektorów finansowych zakładów. Galopujące ceny energii elektrycznej uderzyły najbardziej w przedsiębiorców, których nie chronią żadne „tarcze” czy ustawy zamrażające ceny. Rosnące ceny za 1 MWh pociągają za sobą drastyczne zmiany kosztów procesów, szczególnie tych energochłonnych. Takim procesem, jeszcze kilka lat temu pomijalnym z punktu widzenia ekonomii zakładu, jest wytwarzanie sprężonego powietrza.
W dobie rosnących cen energii, sprężarki generują znaczące koszty dla zakładu, a sprężone powietrze stało się po prostu medium kosztownym. Patrząc na koszty energii z tej perspektywy należy zadać sobie pytanie – w jakim stopniu jesteśmy w stanie zoptymalizować proces zużycia sprężonego powietrza oraz zminimalizować występowanie jego strat? Na pomoc przychodzą ultradźwiękowe metody wykrywania nieszczelności w instalacjach sprężonych gazów. Przyjrzyjmy się więc procedurze szukania nieszczelności, ich lokalizacji oraz określania wielkości strat za pomocą ultradźwięków.
WYCIEKI SPRĘŻONEGO POWIETRZA
Sprężone powietrze to powietrze o ciśnieniu wyższym niż początkowe (atmosferyczne), wytwarzane przy użyciu specjalistycznych urządzeń nazywanych sprężarkami powietrza. W zależności od przyszłych zastosowań oraz wymaganej jakości i czystości sprężonego powietrza, stosuje się sprężarki o różnej konstrukcji i specyfikacji. Dzięki swoim właściwościom sprężone powietrze ma szerokie zastosowanie w wielu gałęziach przemysłu.
Wykorzystywane jest głównie jako medium do zasilania urządzeń pneumatycznych takich, jak: pistolety lakiernicze, szlifierki, przecinarki, klucze udarowe, siłowniki itp.
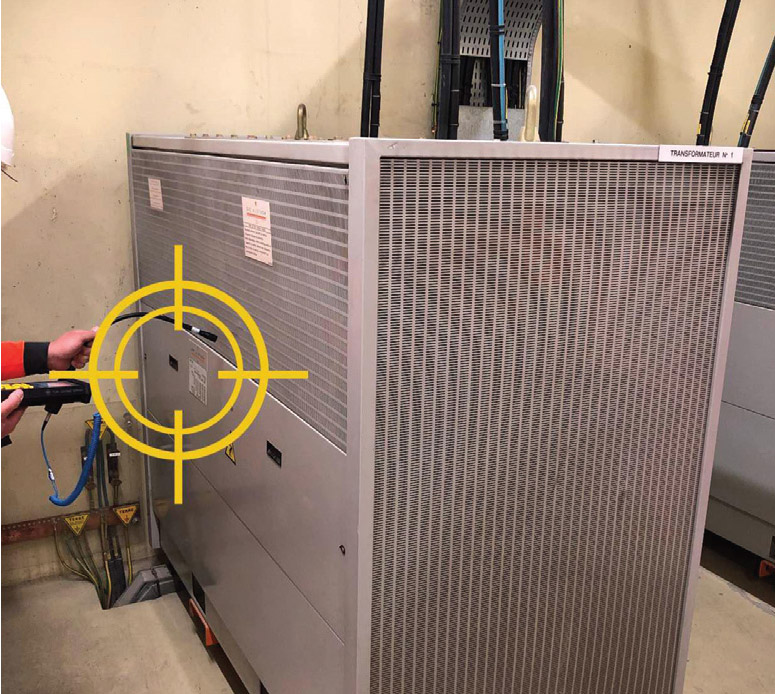
Rysunek 1
Przemysłowa sprężarka powietrza
W odróżnieniu do energii elektrycznej, gazu czy wody, sprężone powietrze jest wytwarzane głównie na miejscu, w danym zakładzie. Co za tym idzie, powinniśmy mieć pełną kontrolę nad instalacją. Z naszego doświadczenia wiemy jednak, że w wielu zakładach nadal występuję niewłaściwa praktyka użytkowania, nadzoru oraz konserwacji linii ze sprężonym powietrzem. To prowadzi do generowania kosztów, które możemy minimalizować. Przykładowo, zakład, który ignoruje prawidłową kontrolę działania instalacji sprężonego powietrza odnotowuje straty na poziomie 20-30% wydajności sprężarki. W przypadku proaktywnego działania, czyli detekcji wycieków sprężonego powietrza (wykrywania nieszczelności) i ich usuwania, straty mogą spaść poniżej 10% mocy sprężarki.
Bardzo ważną sprawą jest zrozumienie przez przedsiębiorstwo, ile potencjalnych strat niesie za sobą złe nadzorowanie linii ze sprężonym powietrzem. Spora rzesza pracowników nie posiada odpowiedniej wiedzy (gdyż nigdy nie była przeszkolona) na temat kosztów oraz prawidłowej praktyki użytkowania instalacji. W konsekwencji dochodzi do defektów takich jak mikropęknięcia na zużytych wężach, złączach, rurociągach czy uszczelnieniach. Mogą one znajdować się w punktach przyłączeniowych czy też w trudno dostępnych miejscach np. za maszynami lub rurociągach umiejscowionych przy sufi cie hali produkcyjnej.
Wycieki sprężonego powietrza są trudne w wykrywaniu, gdyż są bezwonne, bezbarwne. Bardzo często są niesłyszalne pośród dźwięku pracujących maszyn i urządzeń na halach produkcyjnych. Dlatego osoby pracujące w służbach utrzymania ruchu często je ignorują, ponieważ nie powodują zauważalnego zagrożenia życia czy też niepowołanego zatrzymania linii produkcyjnej.
Jednak wycieki, mimo iż niegroźne, bywają bardzo kosztowne. Jak długo nie zmienimy postrzegania kłopotu wycieków sprężonego powietrza jako problemu priorytetowego, tak długo przedsiębiorstwa będą ponosić straty, które można zminimalizować.
DETEKCJA WYCIEKÓW SPRĘŻONEGO POWIETRZA – METODY WYKRYWANIA NIESZCZELNOŚCI
Tradycyjna metoda detekcji wycieków sprężonego powietrza opiera się na nasłuchiwaniu charakterystycznych, syczących dźwięków. Metoda ta ma wiele wad – między innymi wykrywa jedynie wyraźne nieszczelności, a w miejscach o dużym poziomie hałasu jej skuteczność jest ograniczona. Kolejnym ograniczeniem jest nasz ośrodek słuchu – ucho, który działa w paśmie od 50 Hz do maksymalnie 20 kHz. Następną z metod jest tzw. pianka do detekcji nieszczelności. Newralgiczne miejsce, głównie połączenie węża/rury, gdzie może zachodzić ryzyko nieszczelności, spryskuje się preparatem z odległości około 40 cm. Jeśli w tym miejscu znajduję się nieszczelność, będą tworzyć się pęcherzyki powietrza.
Procedura ta jest bardzo czasochłonna i wymaga angażowania sporej grupy ludzi, aby udało się skontrolować instalację znajdującą się na całym zakładzie. W praktyce, w większości przypadków jest to niemożliwe do wykonania we wszystkich miejscach, w których może dojść do wycieku. Ostatnią metodą jest wykrywanie nieszczelności na podstawie ultradźwięków. Ultradźwięki są to fale dźwiękowe o częstotliwości powyżej 20 kHz, czyli są niesłyszalne dla człowieka.
Nieszczelności, poprzez przepływ turbulentny, w miejscu wycieku generują niesłyszalne dla nas ultradźwięki. Właśnie dlatego za pomocą ultradźwiękowych mierników oraz specjalistycznych kamer jesteśmy w stanie bez problemu zlokalizować miejsce i poziom defektu.
Detekcja wycieków sprężonego powietrza za pomocą mierników ultradźwiękowych
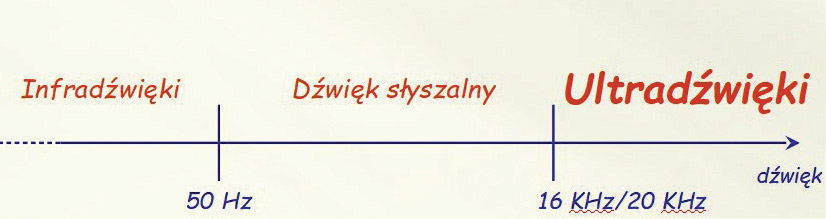
Rysunek 2
Zakres częstotliwości dźwięku
Mierniki ultradźwięków to wielofunkcyjne urządzenia pozwalające na detekcję, pomiar oraz rejestrację ultradźwięków. Te innowacyjne mierniki są wykorzystywane w wielu obszarach dotyczących szczególnie pracy działu utrzymania ruchu. Przyrządy te pozwalają kontrolować i analizować pracę łożysk, odwadniaczy, zaworów, przekładni oraz inspekcję elektryczną instalacji o napięciach powyżej 2 kV w kierunku wyładowań niezupełnych. Jednym z ich głównych zastosowań jest także wykrywanie przecieków sprężonego powietrza.
Mierniki przetwarzają sygnał ultradźwiękowy na dźwięk słyszalny dla człowieka.
Mierniki przetwarzają sygnał ultradźwiękowy na dźwięk słyszalny dla człowieka, dlatego zestaw z reguły posiada słuchawki. Przyrządy wyposażone są w kolorowy wyświetlacz oraz kilka przycisków funkcyjnych. Mierniki w swoim komplecie posiadają pełną game różnych sond pomiarowych. Do detekcji przecieków wykorzystujemy sondy bezkontaktowe:
– Paraboliczna sonda bezkontaktowa – umożliwia pomiar od 2 do 30 m. Szczególnie przydatna podczas przeprowadzania kontroli układów sprężonego powietrza znajdujących się poza zasięgiem „ręki” – na wysokości, np. przy suficie hali. Sonda ma wbudowany wskaźnik laserowy oraz muszkę szczerbinkę, aby dokładnie wskazać miejsce wycieku.
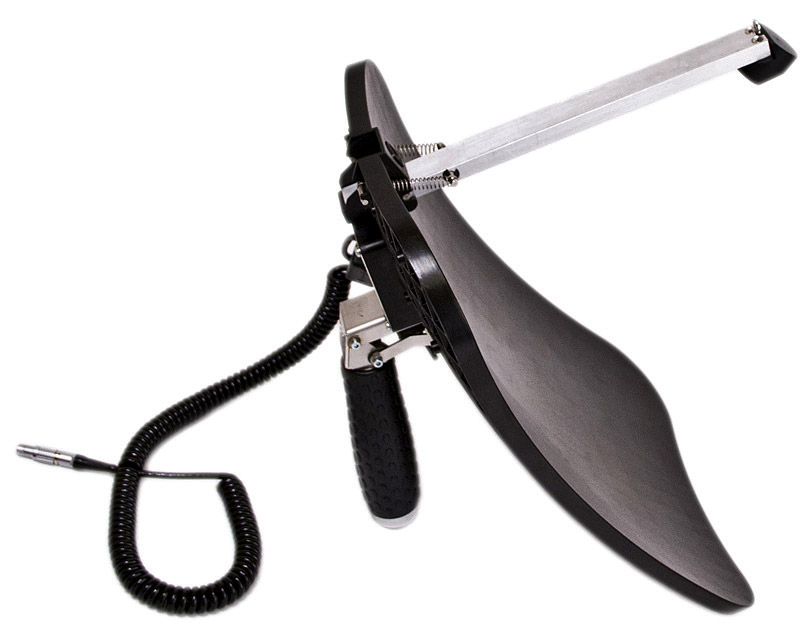
Rysunek 4
Paraboliczna sonda bezkontaktowa
– Elastyczna sonda bezkontaktowa – druga z sond wykorzystywanych przy kontroli nieszczelności. Przyrząd ma elastyczną szyjkę zakończoną ultradźwiękowym mikrofonem o średnicy 16 mm. Sondę możemy dowolnie wyginać tak, aby umożliwić wygodny pomiar. Należy ją jednak chronić przed zanieczyszczeniami, szczególnie płynami, które mogą obniżyć czułość mikrofonu.
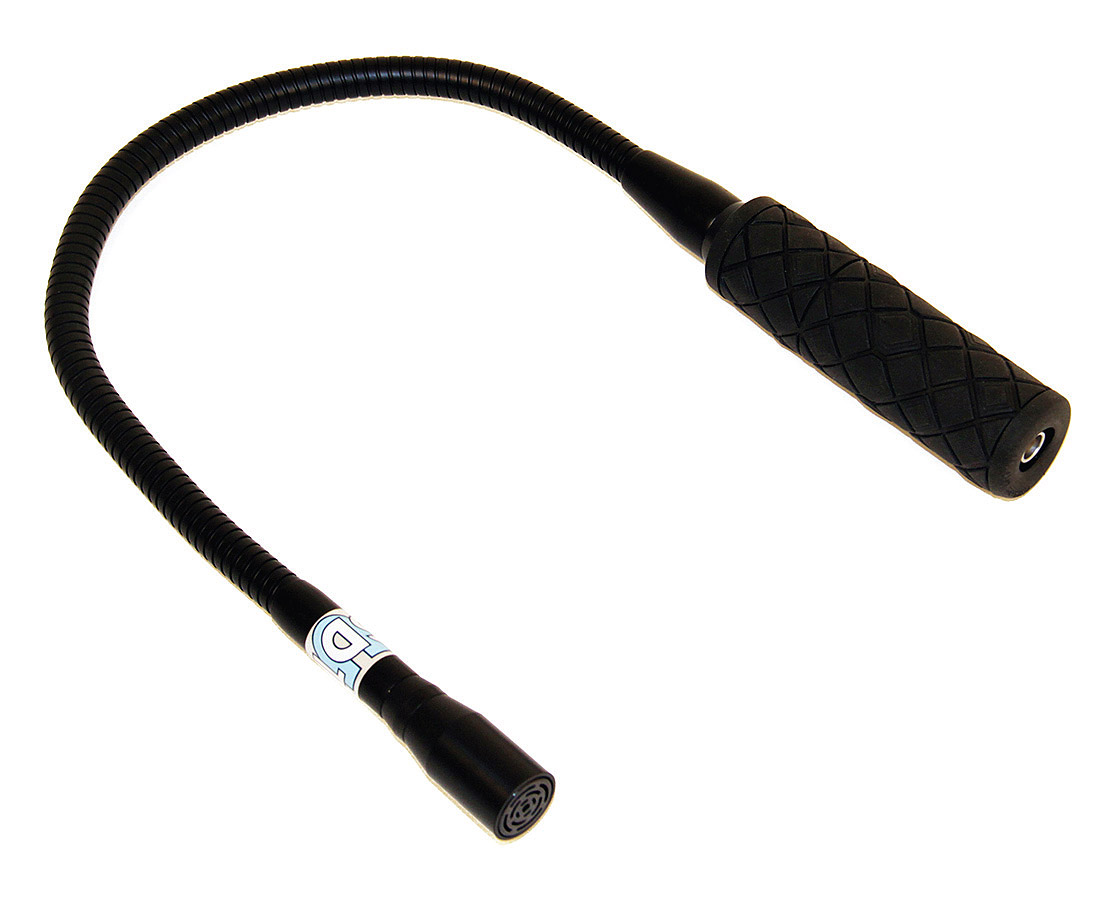
Rysunek 5
Elastyczna sonda bezkontaktowa
Wykonywanie kontroli przy użyciu mierników polega na dokładnym skanowaniu instalacji sprężonego powietrza za pomocą sond bezkontaktowych. Podczas pomiarów z reguły używamy podłączonych do miernika słuchawek, dzięki którym będziemy słyszeć przetworzony sygnał ultradźwiękowy. Na wyświetlaczu urządzenia będzie się również pokazywał poziom ultradźwiękowy w dBmV. Mierniki będą wyświetlać na ekranie informacje dotyczące zmniejszenia lub zwiększenia wzmocnienia poziomu
ultradźwięków, dostosowując się do poziomu hałasu środowiska pracy. Hałas wytwarzany przez pracujące maszyny będzie ignorowany.
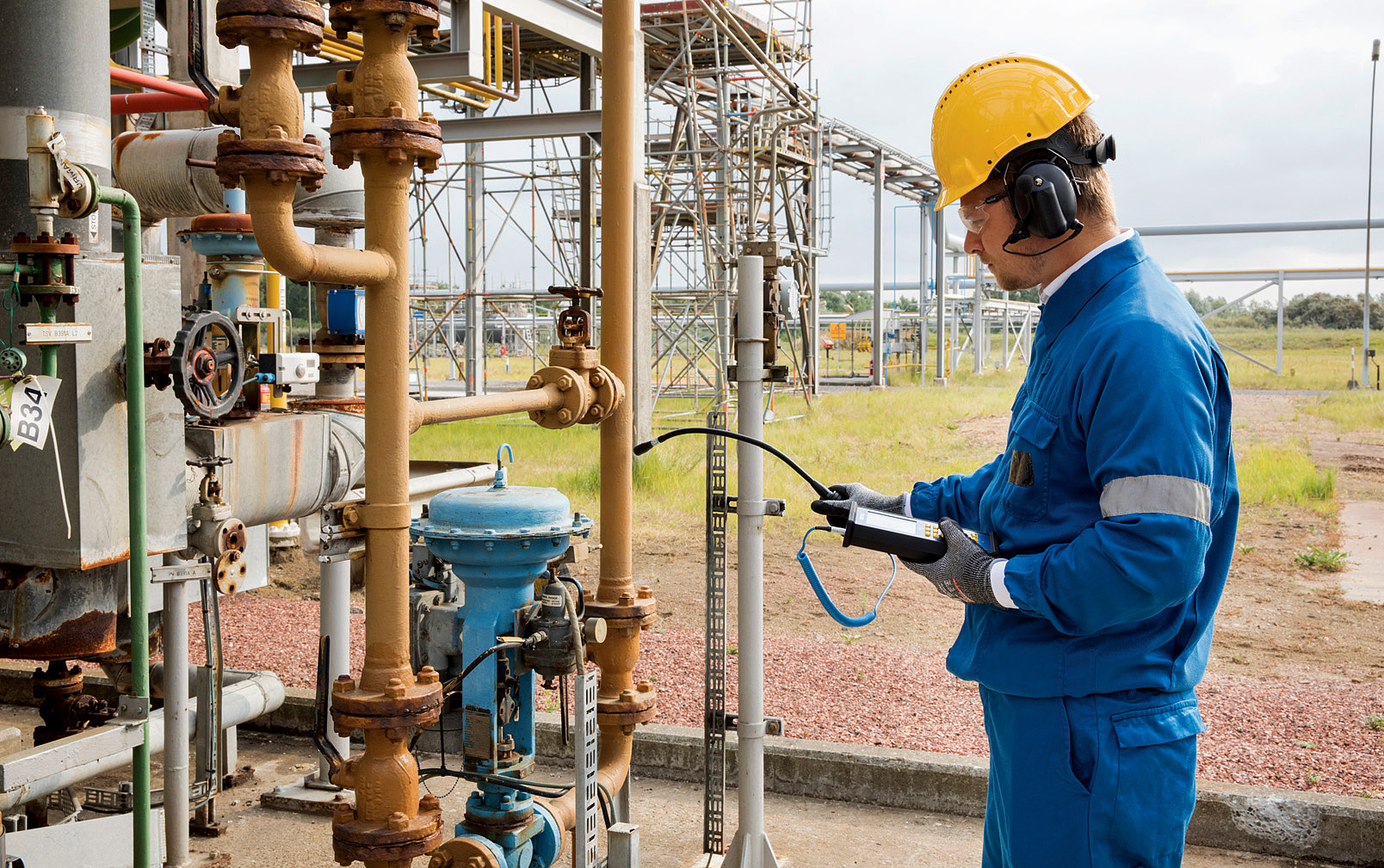
Rysunek 6
Detekcja wycieków sprężonego powietrza przy użyciu miernika SDT 340
Skanując instalację szukamy najwyższego poziomu ultradźwięków, który jest charakterystyczny dla wycieków. Dzięki temu uda nam się dokładnie zlokalizować defekty powodujące wycieki sprężonego powietrza.
Za pomocą ultradźwiękowych mierników oraz kamer akustycznych jesteśmy w stanie szybko zlokalizować miejsce i poziom wycieku.
ULTRADŹWIĘKOWE KAMERY AKUSTYCZNE
Obok mierników ultradźwięków mamy także do dyspozycji kamery akustyczne. Są to przenośne, przemysłowe rejestratory akustyczne obsługujące pasmo częstotliwości ultradźwięków.
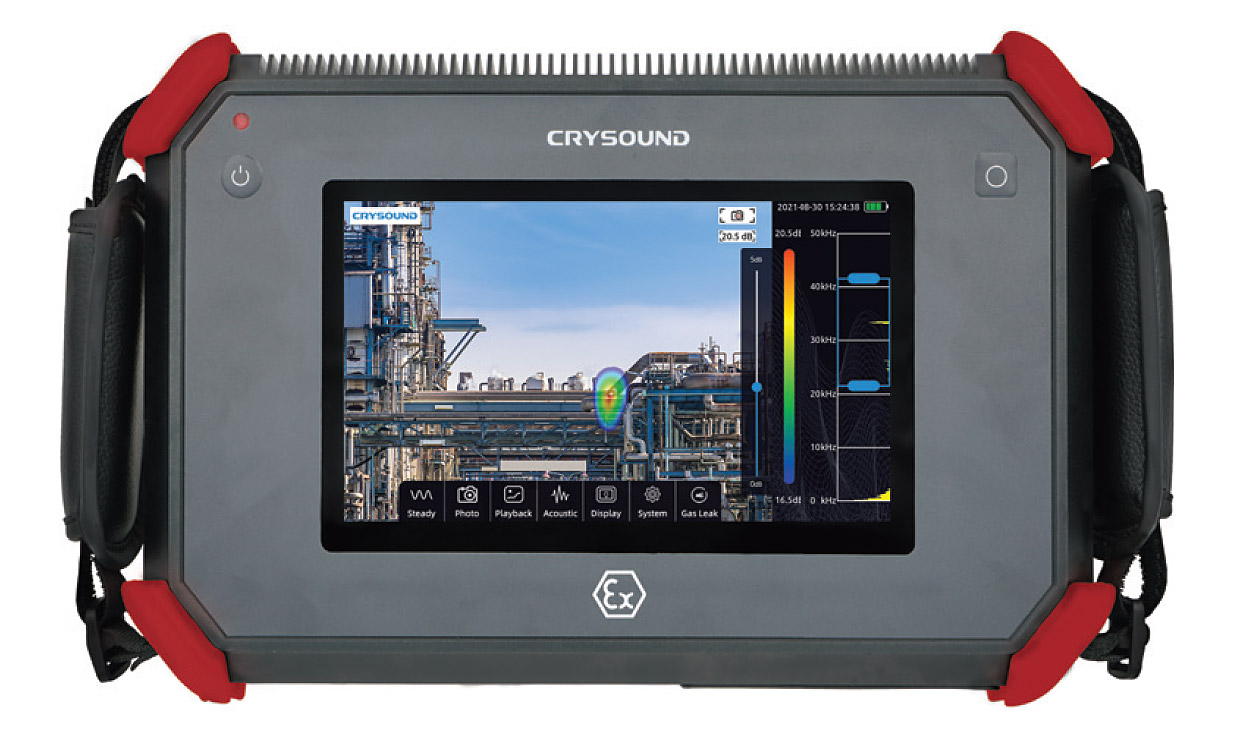
Rysunek 7
Kamera akustyczna CRYSOUND – wyświetlacz
Kamery wykorzystują specjalnie ukształtowaną matrycę mikrofonów wykonanych w technologii MEMS do gromadzenia danych o natężeniu emisji źródeł dźwięku. W kamerze o wysokiej rozdzielczości dźwięki te nanoszone są na obraz wideo w czasie rzeczywistym. Przemysłowe kamery akustyczne pomagają szybko wykryć wycieki gazu pod ciśnieniem i próżni w hałaśliwych instalacjach przemysłowych. Zasięg detekcji wycieków waha się w granicach od 0,3 m do aż 120 m.
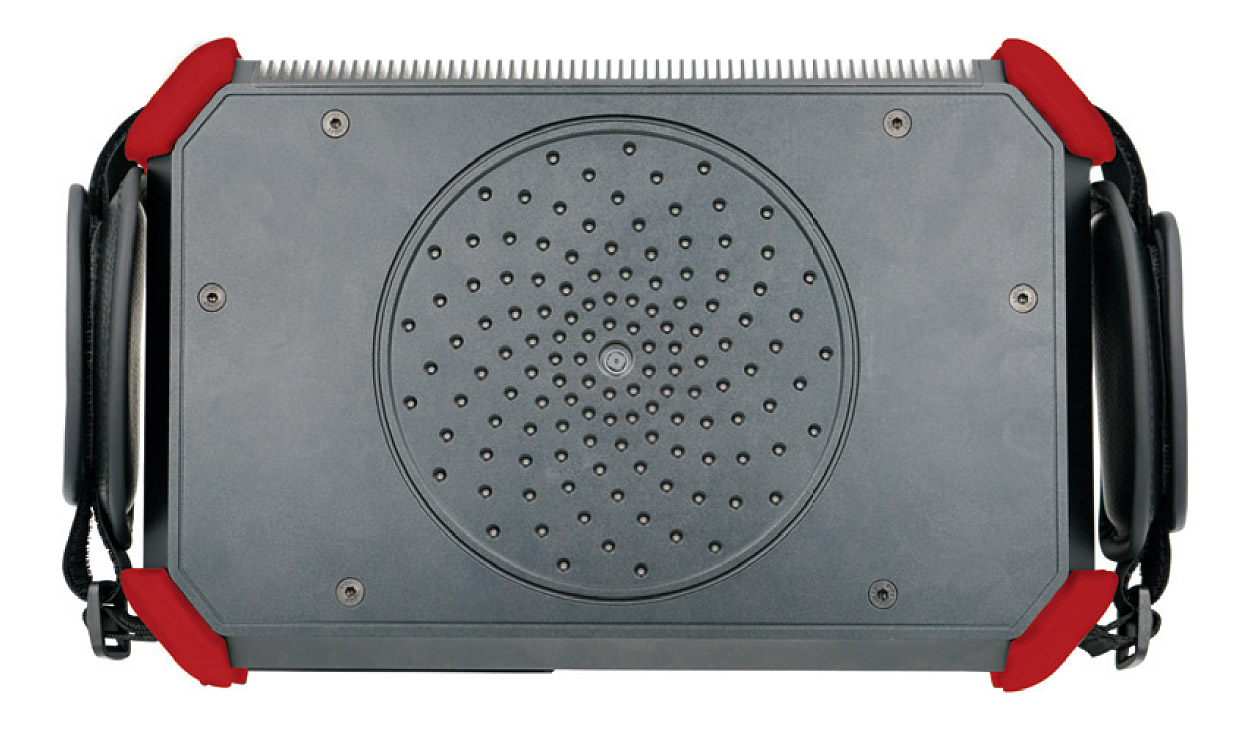
Rysunek 8
Kamera akustyczna CRYSOUND – matryca mikrofonów MEMS
Przeprowadzanie kontroli wycieków kamerami akustycznymi wykonujemy bardzo podobnie jak w przypadku mierników ultradźwięków, dokładnie skanując instalację sprężonego powietrza. W trakcie przeprowadzania audytu musimy dostosować dwa parametry: zakres częstotliwości testowej oraz zakres dynamiki testu. Natomiast sygnał ultradźwiękowy jest przetwarzany na obraz widzialny w formie kolorowych „plam” w miejscu występowania nieszczelności. W momencie znalezienia wycieku możemy bezproblemowo wykonać i zapisać zdjęcie lub nagrać film. Kamery akustyczne dają nam więc możliwość szybkiej lokalizacji nieszczelności oraz przeskanowania bardzo dużej powierzchni w krótkim czasie.
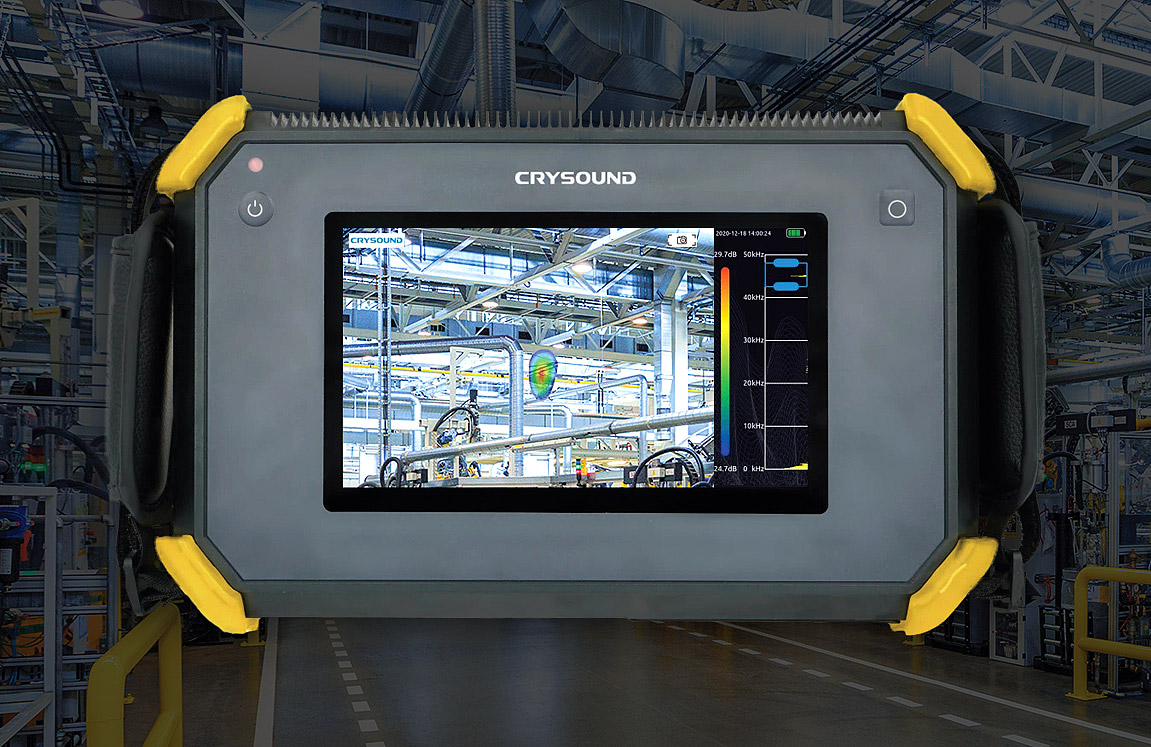
Rysunek 9
Wyciek zobrazowany w kamerze akustycznnej CRYSOUND
APLIKACJA DO TWORZENIA RAPORTÓW
Aby ułatwić pracę osobom nadzorującym instalację sprężonego powietrza, stworzono aplikację mobilną na smartfony i platformy internetowe, do rejestrowania oraz generowania raportów pokazujących poziom wycieków po wykonaniu audytu w danej fabryce. Po zebraniu danych z przeglądu linii zarówno na platformie internetowej, jak i w aplikacji mobilnej, można dokonać przeglądu wykonanej pracy, rzeczywistych i potencjalnych oszczędności w złotówkach i ilość strat powietrza w m³/h.
Kamery akustyczne dają nam możliwość szybkiej lokalizacji nieszczelności oraz przeskanowania bardzo dużej powierzchni w krótkim czasie
Można również zobaczyć datę, kiedy audyt miał miejsce oraz które ze znalezionych nieszczelności zostały już naprawione, a które dalej pozostają bez naprawy. Jak wprowadzać dane do aplikacji? Przed wykonywaniem przeglądu musimy znać i wprowadzić kilka istotnych informacji dotyczących specyfikacji technicznej układu ze sprężonym powietrzem w danej fabryce. Są to: wydajność sprężarki, cena za 1 kW energii elektrycznej, przypuszczalna ilość godzin, w których instalacja jest w trakcie pracy oraz ciśnienie robocze. Wszystkie te informacje wprowadzamy do aplikacji tworząc „nowy przegląd”.
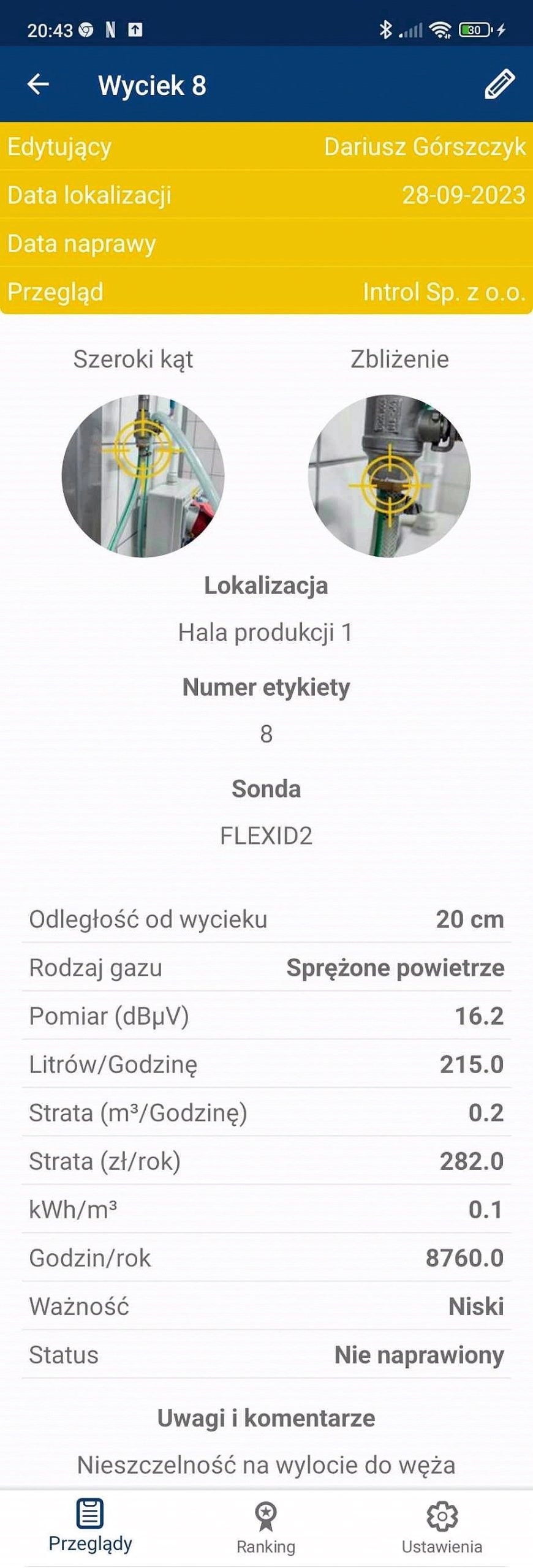
Rysunek 10
Przykładowy wyciek w aplikacji LEAKreporter
Wszystkie te informacje wprowadzamy do aplikacji tworząc „nowy przegląd”. Wprowadzenie danych w aplikacji jest bardzo intuicyjne, zgodnie z opisanymi „okienkami”. Jeśli posiadamy powyższe dane i są one zapisane w aplikacji, to możemy przejść do wykonywania przeglądu nieszczelności miernikami ultradźwięków lub kamerami akustycznymi. W momencie znalezienia nieszczelności, otwieramy aplikację, wykonujemy dwa zdjęcia (z daleka i bliska), opisujemy miejsce na hali, w którym się znajdujemy, następnie wpisujemy wartość liczbową z wyświetlacza miernika – zapisujemy znaleziony wyciek. Możemy już w tym momencie sprawdzić jak duży jest to wyciek w m³/h oraz ile tracimy złotówek w ciągu roku. Analogicznie zapisujemy kolejne znalezione wycieki. Po przeprowadzeniu całego audytu możemy przejść do generowania raportu w formacie pdf. Raport ten będzie zawierał wszystkie zapisane dane oraz znalezione wycieki z opisami i określoną ilością strat. Aplikacja podsumuje całkowitą wartość strat w m³/h oraz straty finansowe wyrażone w danej walucie.
MIERZ, RAPORTUJ, OSZCZĘDZAJ, czyli kontrola szczelności instalacji sprężonego powietrza kluczem do oszczędności
Sprężone powietrze jest jednym z bardzo ważnych mediów wykorzystywanym w zakładach przemysłowych. Jest ono wytwarzane głównie na miejscu dzięki odpowiednio dobranym sprężarkom. Koszt wyprodukowania sprężonego powietrza jest stosunkowo wysoki, dlatego też prawidłowa kontrola działania oraz konserwacja instalacji ze sprężonym powietrzem są niezmiernie istotne z punktu widzenia optymalizacji procesów.
Systematyczna detekcja wycieków sprężonego powietrza może znacząco obniżyć koszty związane z eksploatacją tego medium.
Prawidłowo przeprowadzona, systematyczna diagnostyka instalacji może znacząco obniżyć koszty związane z eksploatacją sprężonego powietrza i ograniczyć powstawanie generujących straty nieszczelności. W przeglądach instalacji pomogą nam urządzenia ultradźwiękowe – zarówno mierniki ultradźwięków, jak i akustyczne kamery. Przyrządy te są bardzo intuicyjne i proste w obsłudze. Dzięki oprogramowaniu jesteśmy w stanie tworzyć szczegółowe raporty, katalogować wycieki, które znaleźliśmy podczas przeglądu. Dane te w każdej chwili możemy analizować, pozwala nam to na podejmowanie kroków dotyczących napraw poszczególnych defektów.
Warto przy tym zaznaczyć, że wartości zawarte w raporcie są przyjmowane jako szacunkowe, a do dokładnego obliczenia kosztów strat wycieków służą przepływomierze (w tym te rozliczeniowe).
Metody ultradźwiękowe natomiast znacznie ułatwią nam dobrą praktykę dbania o instalację ze sprężonym powietrzem i zdecydowanie obniżą koszty eksploatacji tego medium. Oczywiście można praktykować starsze metody wykrywania nieszczelności, ale są one mało miarodajne, słabo wydajne i bardzo czasochłonne.
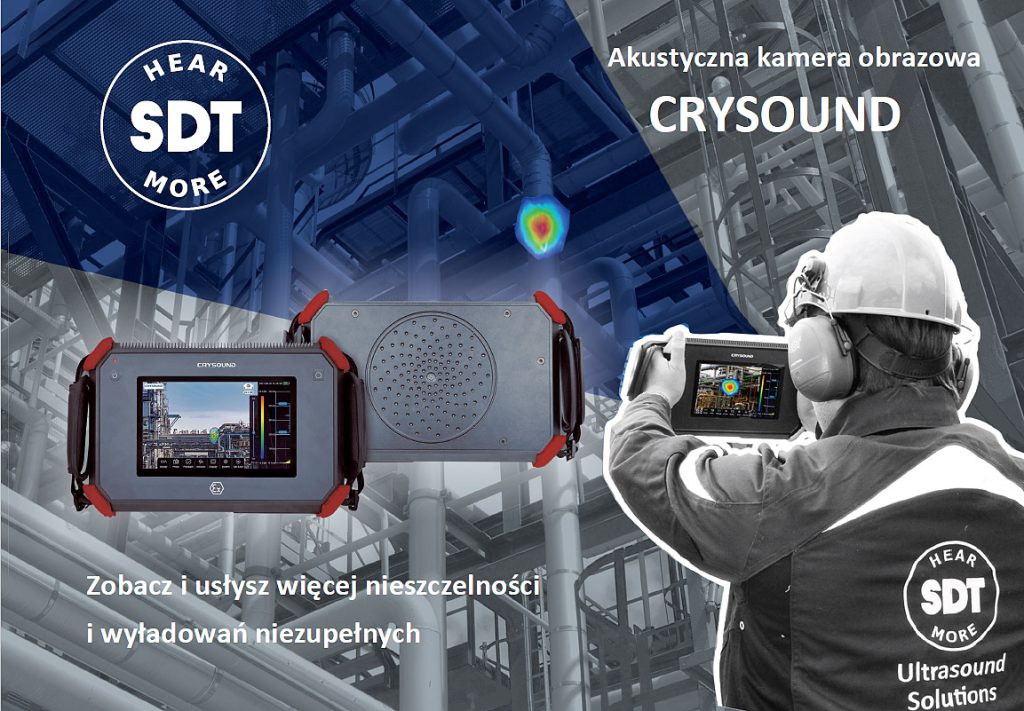