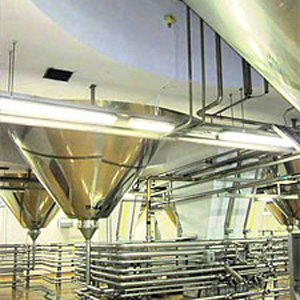
Nic nie gasi pragnienia tak jak zimne jasne pełne lub, jeśli ktoś woli, ciemne mocne. Kto z nas jednak zastawia się jak przebiega proces warzenia piwa i tym samym z jakimi niebezpieczeństwami piwowar ma do czynienia na co dzień? Czy wiemy jakie niebezpieczne substancje wykorzystywane są przy masowej produkcji naszego ulubionego złocistego napoju? Czy zdajemy sobie sprawę jak złożony musi być system detekcji gazów aby był skuteczny? Przyjrzyjmy się zatem jak systemy detekcji zapewniają bezpieczeństwo podczas całego procesu warzenia piwa.
PIWO CHŁODZIMY AMONIAKIEM
Piwo warzone jest na świecie od ponad 6 tysięcy lat. Na przestrzeni wieków i w różnych regionach świata mnogość jego gatunków jest tak liczna, że nie sposób jest je jakkolwiek sklasyfikować. Proces technologiczny produkcji zmieniał się na przestrzeni lat, a w zależności od gatunku produkowanego piwa niektóre jego etapy trwają dłużej, inne są zupełnie pomijane. Generalnie jednak proces produkcji rozpoczyna się przygotowaniem brzeczki, kolejno następuje jej warzenie, fermentacja przy udziale drożdży, leżakowanie i finalnie rozlew piwa do butelek, puszek i kegów.
Podczas fermentacji wytwarzany jest dwutlenek węgla nadający piwu bardzo dobrze znane wszystkim bąbelki (podobno odpowiedzialne za szum w głowie) oraz pianę (koniecznie na dwa palce). Zarówno w procesie fermentacji, jak i leżakowania niezbędne jest zachowanie stałej, niskiej temperatury produktu. Wartości temperatur zależą także od gatunków piwa jakie są warzone i mają kluczowy wpływ na jego kolor, zawartość alkoholu, a przede wszystkim smak. Właśnie z uwagi na ten ostatni parametr, szczególną uwagę poświęca się w browarze instalacji chłodniczej, w której czynnikiem chłodzącym jest amoniak.
Należący do Kompani Piwowarskiej Browar w Tychach sąsiaduje bezpośrednio ze Śląską Giełdą Kwiatową. Z uwagi na niebezpieczeństwo zagrożenia związanego z możliwością przedostania się chmury amoniaku na teren Śląskiej Giełdy Kwiatowej, Inspektorat Ochrony Środowiska zalecił zastosowanie systemu mającego na celu zapobiec takiemu zajściu.
Powstały projekt techniczny zakładał realizację trzech odrębnych systemów mających na celu:
- wykrycie wycieku amoniaku,
- stworzenie kurtyny wodnej pochłaniającej amoniak,
- odprowadzenie wody amoniakalnej do zakładowej oczyszczalni ścieków.
Integracja w/w systemów została zrealizowana poprzez sterownik PLC będący nadrzędnym elementem systemu detekcji. Nasi inżynierowie opracowali algorytm sterujący pracą zraszaczami oraz systemami klap kanalizacyjnych.
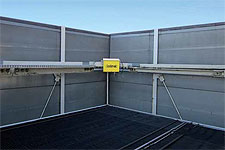
Detektor NH3 w rejonie skraplania
SYSTEM DETEKCJI AMONIAKU W REJONIE TANKÓW GK3, GK4 ORAZ SKRAPLACZY
Każdy z 3 obiektów wyznaczonych do objęcia detekcją został podzielony na strefy w celu zapewnienia najdokładniejszej lokalizacji miejsca wycieku oraz neutralizacji toksycznej chmury amoniaku. W celu zapewnienia szybkiego i precyzyjnego wykrycia wycieku amoniaku z instalacji chłodniczej, zastosowano detektory mierzące stężenie NH3 w zakresie 1000 ppm. Wykrycie niższych stężeń (wartości określanych w Rozporządzeniu przez Ministra Gospodarki jako NDS – Najwyższe Dopuszczalne Stężenie) na zewnątrz budynków jest bardzo trudne do zrealizowania, ponieważ amoniak jako gaz lżejszy od powietrza bardzo szybko zaczyna się unosić. Dlatego też detektory zostały zamontowane bezpośrednio nad miejscami potencjalnych wycieków – tj. w rejonie zaworów instalacji chłodniczej.
Detektory zostały dodatkowo umieszczone w specjalnych osłonach pogodowych chroniących je przed warunkami atmosferycznymi i wodą rozpylaną z instalacji zraszaczy podczas wykrycia wycieku. Z uwagi na rozległość instalacji punkty pomiarowo-zraszające zostały wybrane w najbardziej newralgicznych miejscach ze szczególnym uwzględnieniem strony zewnętrznej Browaru graniczącego ze Śląską Giełdą Kwiatową.
SYGNALIZACJA I WIZUALIZACJA
Kluczowym elementem systemu detekcji i monitoringu gazów jest dotykowy panel operatorski stanowiący interfejs komunikacyjny pomiędzy wszystkimi parametrami systemu a Operatorem. Jego zastosowanie umożliwia graficzną prezentację punktów pomiarowych na dostarczonych przez Inwestora rzutach budowlanych obiektu. Takie rozwiązanie pozwala w sposób szybki i jednoznaczny określić źródło potencjalnego niebezpieczeństwa oraz niezwłocznie podjąć działania mające na celu usunięcie awarii powodującej wyciek amoniaku. Cyfrowy system detekcji oparty na sterowniku PLC pozwolił na zastosowanie lokalnych central komunikacyjno-sterujących odpowiedzialnych za pracę miejscowej sygnalizacji optyczno-akustycznej. Centrale miały także za zadanie wysyłanie informacji do podsystemów współzależnych tj. systemu zraszaczy oraz systemu sterowania zasuwami kanalizacyjnymi.
Powstały w Browarze w Tychach system integrujący pracę trzech niezależnych systemów jest jedynym takim system w Polsce. Nadmienić należy także, że podobne, zrealizowane przez nas systemy detekcji pracują także w browarze w Żywcu oraz Elblągu, jednak tam nie współpracują one z instalacją zraszaczy.
WYMIANA SYSTEMU DETEKCJI W HALI FERMENTACJI
Pomimo, iż realizacja projektu w Tychach nie odbyła się bez problemów (podczas prac montażowych temperatura powietrza sięgała nawet -20°C), Inwestor będąc zadowolony zarówno z funkcjonalności systemu jak i realizacji projektu jako całości, powierzył naszej firmie także wymianę systemu detekcji amoniaku oraz dwutlenku węgla na hali fermentacji ZKT4.
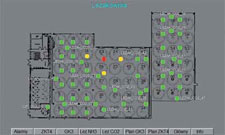
Zrzut ekranu z panelu operatorskiego
Realizacja systemu detekcji w hali fermentacji znacznie różniła się od poprzedniego systemu wykonanego na terenie Browarów Tyskich. Przede wszystkim niezbędne okazało się zainstalowanie odrębnej centrali systemu detekcji, ponieważ ten etap produkcji podlega innemu wydziałowi technologicznemu. Detekcja amoniaku wewnątrz hali, w której mogą przebywać pracownicy wymaga także innych zakresów pomiarowych. Zastosowano progi detekcji odpowiadające wartościom NDS oraz NDSch określonych w przepisach dotyczących dopuszczalnych wartości stężeń w środowisku pracy. Dodatkowo należało zintegrować systemem z zakładowym systemem wentylacji w celu zapewnienia należytej wymiany powietrza w przypadku wykrycia niebezpiecznych stężeń wewnątrz hali. Detekcja wycieku amoniaku z instalacji chłodniczej w halach fermentacji nie jest jednak głównym zagrożeniem dla obsługi instalacji technologicznej. Znacznie większe niebezpieczeństwo związane jest z pojawianiem się wysokich stężeń dwutlenku węgla podczas rozszczelnienia i opróżniania tanko fermentatorów. Dwutlenek węgla jako gaz cięższy od powietrza gromadzi się bezpośrednio nad posadzką oraz w kanałach zrzutowych instalacji. Wykrycie substancji gromadzącej się w określonych miejscach tylko z pozoru wydaję się być łatwiejsze.
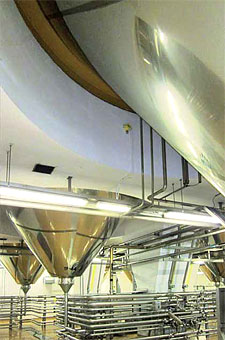
Detektor NH3 w hali
W celu zapewnienia najwyższych standardów sanitarnych oraz bhp wszystkie hale oraz instalacje technologiczne na terenie browaru myte są bowiem cyklicznie metodą wysokociśnieniową. Dlatego też urządzenia instalowane na terenie hal produkcyjnych wymagają stopnia ochrony nie niższego niż IP 66, a to z kolei wiąże się z problemami natury pomiarowej.
Aby zapewnić skuteczne wykrycie pojawienia się jakiegokolwiek gazu urządzenie do jego detekcji nie może być bowiem idealnie szczelne, ponieważ uniemożliwi to migrację gazu do sensora. Standardowo stosowane osłony bryzgoszczelne mające chronić spiek detektora przed zachlapaniem niestety nie sprawdziły się. Podczas testów wykonanych na terenie browaru okazało się, iż osłony te nie są w stanie zabezpieczyć właściwie sensora przed zalaniem.
Specjalnie na potrzeby instalacji w browarze osłony bryzgoszczelne zostały przeprojektowane w taki sposób, aby zapobiec zalaniu sensora zarówno poprzez bezpośrednie strugi wody oddziaływające na głowice sensora, jak również na strumień odbity np. od posadzki.
Tak skonstruowane osłony z powodzeniem chronią sensory przed szkodliwym działaniem wody, a jednocześnie umożliwiają swobodną wymianę powietrza – nie spowalniając reakcji sensora na dwutlenek węgla.
Panel operatorski zastosowany w systemie detekcji hali ZKT4 oprócz graficznej prezentacji obiektu monitorowanego, zapewnia także rejestrację zdarzeń –np. przekroczenia zdefiniowanych stężeń, awarii, wyłączenia zasilania, a także przekroczonego terminu kalibracji. Funkcjonalność ta ma duże znaczenie szczególnie w przypadku detekcji dwutlenku węgla, którego podwyższone stężenie występuje na terenie hal produkcyjnych kilkukrotnie w ciągu doby. Nie jest to sytuacja awaryjna, lecz związana jest z normalnym przebiegiem procesu technologicznego. Rejestrowanie przekroczeń pozwala zakładowym służbom bhp zweryfikować historyczny stan monitorowanych obiektów. Może mieć to szczególne znaczenie jeżeli na skutek przekroczenia stężenia gazu niebezpiecznego miał miejsce wypadek z udziałem pracowników przebywających w strefie objętej monitoringiem.
PRZYDATNA STACJA OPERATORSKA
Archiwizacja zdarzeń wewnątrz panelu operatorskiego jest narzędziem bardzo pomocnym, jednak informacje zapisywane w historii są bardzo ograniczone, a dostęp do danych archiwalnych jest mało wygodny.
Realizowane przez nas systemy mogą współpracować także z komputerową stacją operatorską zapewniającą pełną rejestrację nie tylko zdarzeń, ale także wartości mierzonych stężeń. Operator może weryfikować wykresy trendów dla poszczególnych hal, generować i drukować raporty o zdarzeniach oraz tworzyć i drukować wykresy trendów w zdefiniowanym czasookresie. Obecnie prowadzone są w browarze rozmowy dotyczące wymiany systemów detekcji w mniejszych obiektach w celu wprowadzenia jednego standardu w całym zakładzie.
Po zakończeniu modernizacji opracowana zostanie propozycja stacji operatorskiej realizującej wizualizację wszystkich systemów w całym browarze z możliwością integracji z systemami kontroli dostępu oraz system ppoż.
SYSTEMY SZYTE NA MIARĘ
Nasza koncepcja systemów detekcji umożliwia stworzenie aplikacji dedykowanej dla danego obiektu i spełniającej nie tylko wymogi prawne, lecz także oczekiwania Inwestora wobec instalowanego systemu. Dzięki temu, że każdorazowo do projektu systemu detekcji podchodzimy indywidualnie, potrafimy dopasować rozwiązanie do potrzeb, wymogów oraz możliwości budżetowych, zapewniając przy tym pełną integrację z posiadanymi systemami nadrzędnymi. Realizacja systemów detekcji w browarze w Tychach jest doskonałym przykładem jak nie tylko jakość i funkcjonalność urządzeń, a przede wszystkim profesjonalny sposób wdrażania systemu przekonuje Inwestora do modernizacji i rozbudowy kolejnych posiadanych systemów. A przecież każda poprawa bezpieczeństwa prowadzonych procesów to sukces zarówno zarządzających jak i pracowników każdego zakładu.
autor:
Adam Goj
agoj@introl.pl