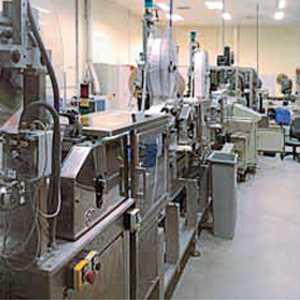
Ilościowe i jakościowe cele stawiane menadżerom produkcji wymagają korzystania z odpowiedniego zaplecza parku maszynowego i linii produkcyjnych. Wymagania ekonomiczne wymuszają optymalizację wydajności procesów technologicznych, czyli zachowania maksymalnej jakości produktu końcowego przy minimalnym zużyciu materiałów i energii. Spełnienie wszystkich wymagań nie jest możliwe bez odpowiednio zaplanowanych i profesjonalnie zrealizowanych modernizacji parku maszynowego, procesów technologicznych, urządzeń i całych linii przemysłowych.
Modernizują, bo muszą
Jedną ze spuścizn minionego systemu jest stan w jakim nierzadko znajdują się maszyny w wielu polskich zakładach. Ich stopień wyeksploatowania bardzo często wydłuża proces technologiczny, obniża jakość produktów końcowych, czy też powoduje przestoje produkcji, przyczyniając się do strat finansowych. To z uwagi na wymagania ekonomiczne, którym nie są w stanie sprostać wyeksploatowane maszyny, ich modernizacja decyduje często o rentowności całej produkcji.
Częstym problemem do rozwiązania przez menadżerów produkcji jest brak integracji poszczególnych elementów linii produkcyjnej. Poszczególne procesy realizowane są w oddzielnych zespołach / elementach, co wiąże się z brakiem optymalnej wydajności całego procesu i większą trudnością w sterowaniu pracą urządzeń. Modernizacja przyczynia się do podniesienia jakości sterowania, co ma przełożenie na zwiększenie wydajności linii technologicznych, a więc finansów firmy.
Innym, często spotykanym problemem jest brak monitoringu i testowania jakości produktu końcowego. Wykonanie odpowiedniej maszyny testującej rozwiązuje te problemy. Wnioski z przeprowadzonych testów umożliwiają optymalizację procesu produkcji oraz otrzymanie produktów o oczekiwanych parametrach.
Wymagania ekonomii oraz zintensyfikowany w ostatnich dwóch dekadach postęp technologiczny to nie jedyne czynniki wpływające na konieczność przeprowadzania modernizacji maszyn i procesów. Ważnym determinatem modernizacji jest konieczność zapewnienia odpowiedniego bezpieczeństwa pracy zgodnie z aktualnymi przepisami i normami. Według danych Głównego Urzędu Statystycznego, 40% wypadków związanych jest z pracami przy obsłudze maszyn i urządzeń*. Poprawa bezpieczeństwa pracy m.in. przy użytkowaniu maszyn, stała się w Polsce jednym z priorytetów w dziedzinie ochrony zdrowia i życia ludzkiego.
Modernizacja 1 – układ sterowania młyna strumieniowego oraz separatora pneumatycznego
Jedną ze zrealizowanych przez nas aplikacji było wykonanie układu sterowania do specjalistycznych urządzeń jakimi są klasyfikatory powietrzne. Z tym problemem zwróciła się do nas firma Comex AS – ekspert w dziedzinie segregacji i separacji materiałów sypkich i sproszkowanych. Comex AS dostarcza rozwiązania systemowe i przemysłowe dla zaawansowanych aplikacji związanych z technologią produkcji i klasyfikacji drobnych cząstek. Wśród urządzeń do przeprowadzenia tego typu procesu, można wyróżnić opatentowane klasyfikatory powietrzne oraz młyny strumieniowe. Różne konfiguracje rozbudowy układów z tego typu urządzeniami wymagają specjalistycznego sterowania.
Młyn strumieniony, klasyfikator…
Młyn strumieniowy pozwala na efektywne rozdrabnianie produktu z możliwością kontroli jego rozkładu na cząstki elementarne. Metoda ta jest używana w odniesieniu do materiałów ściernych lub wtedy, gdy metoda rozdrabniania musi być przeprowadzona w warunkach najwyższej czystości. Przez otwór wlotowy, za pomocą podajnika, materiał podawany jest grawitacyjnie do komory młyna, a następnie umieszczany w obszarze mielenia, w którym znajdują się specjalistyczne dysze. Dysze powietrzne wprowadzają czyste powietrze, dzięki czemu cząstki elementarne materiału przyspieszają do bardzo dużych prędkości.
Przyspieszone cząstki zderzają się w centralnej części komory młyna, co przekłada się na ich zmniejszenie do odpowiednich rozmiarów. Z powodu dekompresji strumienia powietrza, zmielone cząstki przemieszczają się do górnych partii młyna, gdzie znajduje się klasyfikator (separator) powietrzny. Klasyfikator zapewnia bardzo precyzyjne oddzielanie cząstek od siebie, które następnie opuszczają młyn lub ewentualnie poddawane są ponownemu procesowi mielenia.
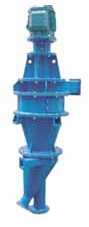
Klasyfikator ACX 200
Drobna frakcja przepływająca przez wirnik opuszcza go wraz z głównym strumieniem powietrza, gdzie następnie jest od niego odseparowywana w cyklonie lub filtrze. W zależności od wymaganego procesu, układ młyn strumieniowy – separator powietrzny może przybierać różne konfiguracje o mniejszej lub większej formie rozbudowy.
Zastosowany układ sterowania
W celu sterowania całym procesem technologicznym, niezbędne było wykonanie odpowiednich szaf sterowniczych zawierających komponenty automatyki przemysłowej. Zastosowano m.in. moduły zasilania, bezpieczniki oraz elektrozawory. Układy wyposażono również w czujniki, przetworniki ciśnienia oraz przetwornice częstotliwości PowerFlex dla silników elektrycznych.
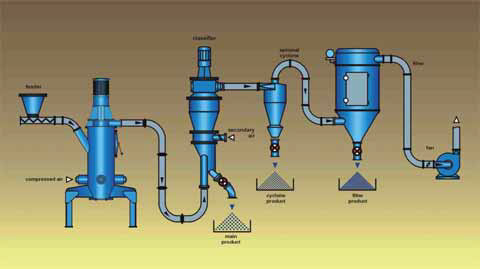
Schemat procesu rozdrabniania i separacji
Elementem zarządzającym jest sterownik PLC MicroLogix 1400 z modułami wejść/wyjść cyfrowych i analogowych. Wykonane szafy sterownicze dostarczono użytkownikom w Norwegii i Chinach oraz do zakładu Comex Polska w Kętach.
Efektem jest…
Przeprowadzona modernizacja pozwoliła na integrację maszyny i urządzeń w jednym systemie. System sterowania pozwala Klientowi na pełną kontrolę przeprowadzanego procesu. Tak wdrożona automatyzacja sterowania procesem znacząco wpływa na jakość i wydajność, minimalizując straty i koszty.
Modernizacja 2 – poprawa jakości i wydajności maszyny pakującej
Z innym problemem zwrócił się do nas Użytkownik branży medycznej, produkujący m.in. plastry chirurgiczne. Brak integracji poszczególnych urządzeń składających się na całość maszyny, powodował niepełne wykorzystanie jej wydajności.
Mając na uwadze optymalizację procesu produkcji, głównym powodem modernizacji maszyny była poprawa jej jakości i wydajności.
Pakowanie plastrów
Modernizacji poddano maszynę pakującą plastry do kartonów. Za pierwszy etap procesu odpowiedzialny jest operator umieszczający rolkę z nawiniętą taśmą z plastrami na odpowiedni wał. W celu ustalenia odpowiedniego naciągu, taśma rozwijana jest na wałki podające, a następnie przekazywana do maszyny. Czujnik sprawdza aktualną pozycję plastrów na taśmie, która kolejno jest pozycjonowana na prawidłową linię cięcia i podawana pod nóż obrotowy. Po zakończonym procesie cięcia, czujniki kontrolują stan techniczny plastrów. Sprawdzana jest prawidłowa długość oraz ewentualne uszkodzenie taśmy, a plastry są zliczane i przemieszczane na tzw. widełki odpowiedzialne za umieszczanie plastrów w pojemnikach znajdujących się na taśmie. Operator jest odpowiedzialny za ilość i rodzaj umieszczanych plastrów w danym pojemniku, w którym to następuje kontrola prawidłowego zapełnienia.
Złe zapełnienie powoduje w dalszym kroku usunięcie z niego plastrów. Kolejnym procesem jest podawanie i rozkładanie kartonów za pomocą ssawek, w celu przygotowania pudełka do załadunku plastrów.
Następuje zrzut plastrów z pojemników do pudełek za pomocą specjalnej szczotki, a następnie klej natryskiwany jest w odpowiednie miejsca kartonu. Końcowym etapem jest składanie oraz zaciskanie pudełka, w którym znajduje się prawidłowa ilość i odpowiedni rodzaj plastrów.
Zmodernizowane sterowanie
Modernizacja układu sterowania linii polegała na wymianie starego sterownika SLC500 na ControlLogix. System sterowania serwosilnikami w technologii GML został wymieniony na rodzinę Kinetix 6000. Do sterowania procesem technologicznym wykorzystano istniejącą wizualizację.
Zmodernizowany system składa się z siedmiu szafek zawierających układ sterowania, układ zasilania, system bezpieczeństwa oraz system serwonapędów wraz z modułami wejść/wyjść. Do połączenia sterownika ControlLogix z serwonapędami zastosowano interfejs Ethernet oraz SERCOS wykorzystujący łącza światłowodowe.
Integracja bardziej wydajna
Przeprowadzona modernizacja umożliwiła Klientowi integrację maszyny i znajdujących się w niej urządzeń w jednym procesie sterowania. Przeprowadzony proces optymalizacji pracy, umożliwił wykorzystanie pełnej wydajności maszyny dla istniejących zasobów. Proces pakowania plastrów został przyspieszony, przynosząc znaczne korzyści finansowe.
Modernizują, bo to się opłaca
Obie wspomniane modernizacje oraz inne, jakie realizowane są w polskich zakładach przyczyniają się m.in. do zwiększenia bezpieczeństwa pracy, poprawy wydajności, optymalizacji procesów technologicznych, monitorowania jakości produktu końcowego oraz minimalizowania czasu przestoju maszyn. Należy oczywiście zawsze wyznaczyć odpowiednie cele przeprowadzenia takich modernizacji oraz określić mierniki jej opłacalności. Tylko wtedy możemy być pewni, iż uzyskane efekty będą potwierdzać zasadność realizacji tego typu inwestycji.
Opisane w artykule realizacje stanowią jedną z licznych modernizacji przeprowadzonych przez dział Systemów Automatyki.
Nasi inżynierowie na co dzień modernizują maszyny i linie produkcyjne, projektują i programują stanowiska badawczo-testujące, czy wreszcie budują prototypowe maszyny pakujące, nawijające itp. Zakres prac jest bardzo zróżnicowany zaczynając od prostych układów automatyki, po złożone systemy automatyzujące całe procesy technologiczne.
* Dane z www.pip.gov.pl