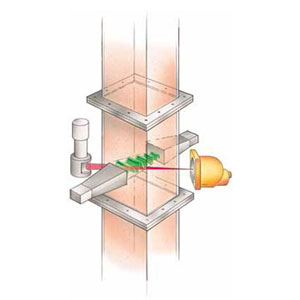
Wszystkie materiały sypkie posiadają swoją wilgotność. Zawartość wody w materiale jest ważna dla wielu procesów produkcyjnych. Woda w materiałach sypkich wpływa na przykład na ich zdolności do przechowywania oraz płynięcie podczas transportu. Ponadto zawartość wody w materiale decyduje często o jakości gotowego produktu. Wszędzie tam gdzie zmiana wilgotności materiału wpływa na dalsze przetwarzanie i podnosi koszty produkcji poprzez wydłużenie procesu suszenia, dodawanie wody, dodatkowe zużycie energii czy większej masy produktu, konieczna jest jej kontrola.
BEZKONTAKTOWY POMIAR MIKROFALOWY
Mikrofalowy pomiar wilgotności jest metodą bezkontaktową, stosowaną w przypadku pomiaru wilgotności materiałów sypkich, nieprzewodzących. Oznacza to, że mierzalnymi są: węgiel, wapno, zrębki drewna, itp., a niemierzalnymi są na przykład koks i grafit. Typowym miejscem aplikacji systemu pomiarowego jest taśmociąg z pasem transmisyjnym wykonanym z materiału nieprzewodzącego, najczęściej z gumy. Kolejnym rozwiązaniem jest zsyp grawitacyjny lub lej zbiornika z odpowiednimi wziernikami wykonanymi ze wspomnianego już materiału nieprzewodzącego, np. teflonu lub ceramiki. System w podstawowej wersji składa się z „mikrofalowej ścieżki pomiarowej” czyli z jednostki sterującej, anteny nadawczej i odbiorczej oraz przewodów łączących anteny z jednostką sterującą. Sygnał mikrofalowy emitowany przez antenę nadawczą przenika przez produkt i dociera do anteny odbiorczej.
Podczas przenikania mikrofal przez produkt występują dwa zjawiska. Pierwszym z nich jest tłumienie, a drugim przesunięcie fazowe nadawanego sygnału. Najczęściej wykorzystywanym w pomiarze jest zjawisko przesunięcia fazowego. Zdarzają się jednakże przypadki kiedy wykorzystywane jest zjawisko tłumienia – pomiar materiałów o dużej zawartości soli. W praktyce bardzo rzadko wykorzystuje się oba zjawiska jednocześnie.
Powyżej schematyczne przedstawienie zmian właściwości mikrofal przechodzących przez produkt:
Wzór opisujący pomiar wilgotności:

gdzie:
Wartość mierzona – wilgotność
A, B, C – współczynniki odpowiedniej funkcji
Bardzo często „mikrofalowa ścieżka pomiarowa” okazuje się niewystarczająca z uwagi na fakt, że sprawdza się ona tylko dla materiału homogenicznego o stałej granulacji i, co najważniejsze, dla zawsze stałej grubości warstwy nasypowej. Jak możemy sobie wyobrazić jest to trudne do uzyskania w praktyce i dlatego potrzebna jest „izotopowa ścieżka pomiarowa”. Służy ona do kompensacji grubości warstwy nasypowej dla taśmociągu lub stopnia wypełnienia materiałem dla zsypu. Do konfiguracji systemu w wersji podstawowej musimy zatem dołączyć pojemnik ze źródłem izotopowym Cs-137 oraz detektor promieniowania gamma.
Poniżej równanie opisujące kompensację grubości warstwy nasypowej:

gdzie:
d – gęstość nasypowa [g/cm3]
d – grubość warstwy materiału [cm]
Pomiar z wykorzystaniem mikrofalowego wilgotnościomierza posiada wiele przydatnych zalet ale nie jest metodą uniwersalną. Możliwość prowadzenia bezkontaktowego pomiaru online, z dobrą dokładnością wynoszącą nawet 0,2% to niewątpliwe korzyści mikrofal. Należy jednak pamiętać o sporych ograniczeniach tej metody jak choćby: wymogi zachowania granulacji maksymalnej wynoszącej 50 mm, mierzalny materiał musi być nieprzewodzący, a wilgotność w postaci lodu jest niemierzalna.
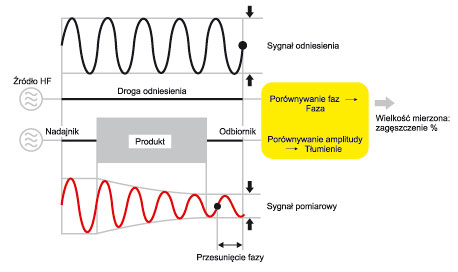
Zmiany właściwości mikrofal przechodzących przez produkt
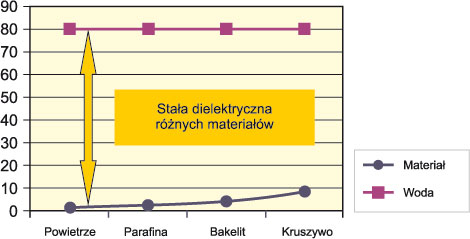
Stała dielektryczna rożnych materiałów
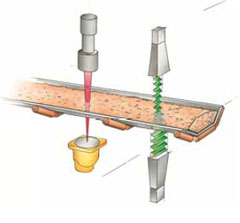
Wilgotnościomierz mikrofalowy LB568 na taśmociągu
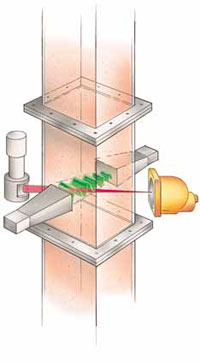
Wilgotnościomierz mikrofalowy LB568 w zsypie
BEZKONTAKTOWY POMIAR NEUTRONOWY
Neutronowa metoda pomiaru wilgotności polega na spowalnianiu szybkich neutronów przez atomy wodoru. Masa neutronu jest w przybliżeniu równa masie atomu wodoru. Inne jądra atomowe są 10-200 razy cięższe.
Szybki neutron trafiając w jadro atomowe o dużej masie doznaje zderzenia, podczas którego traci niewielką ilość energii. Przy zderzeniu z jądrem wodoru neutron traci więcej niż połowę swojej energii. Po kilku zderzeniach z jądrami wodoru neutron szybki staje się neutronem termicznym.
Na skutek rozproszenia neutronów wokół źródła neutronów szybkich powstaje chmura neutronów termicznych, których gęstość maleje wraz z rosnąca odległością. Im większa jest zawartość wodoru w materiale mierzonym tym większa jest gęstość oraz stężenie neutronów wolnych (termicznych) wokół sondy. Wielkość wilgotności materiału jest proporcjonalna do objętościowej zawartości wodoru. Na „hamowanie” wodoru nie mają wpływu temperatura, ciśnienie, wartość pH, granulacja. Należy jednak pamiętać, że elementem zakłócającym pomiar mogą być materiały zawierające w swojej wewnętrznej strukturze atomy wodoru. Pożądanym jest więc aby jedynym materiałem zawierającym wodór była woda, która jest odpowiedzialna za wilgotność materiału. Skutecznym jest zatem pomiar wilgotności materiałów nie zawierających atomów wodoru.
Najczęściej neutronową metodę pomiaru wilgotności stosujemy w pomiarze wilgotności koksu, piasku i rudy żelaza.
Typowy układ pomiarowy składa się z jednostki sterującej, detektora wolnych neutronów wraz ze źródłem szybkich neutronów AmBe. Sonda może być zaaplikowana do rury wgłębnej zabudowanej w zbiorniku i otoczonej mierzonym produktem lub może to być sonda powierzchniowa do zabudowy na ścianie zbiornika. Podobnie jak w przypadku wilgotnościomierza mikrofalowego, do kompensacji zmian ciężaru nasypowego materiału zaleca się zastosowanie pomiaru gęstości używając źródła Cs-137 oraz detektora promieniowania gamma.
Warunkiem koniecznym uzyskania satysfakcjonujących wyników pomiarowych jest zapewnienie sondzie ze źródłem AmBe „kuli pomiarowej” czyli sfery z materiału o średnicy minimum 1m. Sonda ze źródłem stanowi środek sfery. Mikrofale i neutrony wykorzystywane są do bezkontaktowego pomiaru wilgotności w trudnych warunkach ciężkiego przemysłu, hutnictwa, energetyki, przemysłu chemicznego. Z uwagi na to, że metody te wykorzystują źródła izotopowe, ich stosowanie jest zawężone do określonych typów aplikacji. Bardziej ekonomiczną i dostępną do stosowania jest metoda kontaktowa wykorzystująca czujniki pojemnościowe.
KONTAKTOWY POMIAR POJEMNOŚCIOWY
Każdy materiał ma swoją stałą dielektryczną, którą mierzą czujniki pojemnościowe. Dla lepszego zrozumienia zasady działania, można przedstawić bardzo uproszczone wyjaśnienie: woda ma względną stałą dielektryczną około 80, w większości innych materiałów jest to od około 1 do 10. Dla przykładu, piasek posiada stałą dielektryczną pomiędzy 3 a 4. Oznacza to, że istnieje duża mierzalna różnica pomiędzy stałą dielektryczną wody (80 ), a pozostałymi („suchymi”) mierzonymi materiałami (1 do 10).
Różnica ta w sposób bezpośredni określa zawartością wody w materiale, a wynik pomiaru otrzymujemy w postaci standardowego sygnału 0 … 10 V lub 4 … 20 mA (lub też cyfrowego protokołu PROFIBUS). Innymi słowy, im wyższa wilgotność materiału, tym stała dielektryczna jest bliżej wartości 80. Pomiar kontaktowymi czujnikami pojemnościowymi odbywa się na ruchu w czasie rzeczywistym. Materiał przesuwa się po czujniku lub odwrotnie. Sygnał pomiarowy jest dostępny natychmiast – nawet gdy materiał transportowany jest z bardzo dużą szybkością. Wyjście sygnałowe może być skalibrowane na procentowy udział wody w materiale lub też zawartość suchej masy. W zależności od rodzaju materiału i jego właściwości, głębokość pomiaru kształtuje się od około 100 mm do 150 mm w głąb materiału.
Oznacza to, że pomiar odbywa się jednocześnie na powierzchni materiału jak również w jego wnętrzu. Czujniki wykonane są z wysokiej jakości stali i ceramiki przez co są bardzo wytrzymałe. Są one przeznaczone do najtrudniejszych miejsc pomiarowych, mogą być instalowane w istniejących miejscach transportu materiału. Ponadto, pomiar jest niewrażliwy na zmiany barwy czy pH materiału, zawarte w nim minerały lub też zawartość soli. Konstrukcja czujnika jest niewrażliwa na uderzenia, wodę, a nawet na silne wibracje. Czujniki są bardzo proste i bezproblemowe w obsłudze, w większości mierzonych materiałów wystarczy jednorazowa kalibracja (bez konieczności kalibracji okresowej).
Nie bez znaczenia jest również to, że za pomocą wysoko-częstotliwościowego czujnika pojemnościowego możemy określać i kontrolować wilgotność produktu w całym zakresie od 0 do 100%. Korzyści z zastosowania systemu opartego o czujniki pojemnościowe:
- przy ciągłym pomiarze wilgotności istotnie można podnieść i zapewnić wysoką jakość produktu finalnego,
- proces produkcyjny jest monitorowany w sposób ciągły (okresowa kontrola laboratoryjna jest obarczona dużym opóźnieniem),
- proces jest sterowany i regulowany w oparciu o zawartość wody w sposób automatyczny,
- możliwość zastosowania różnych krzywych kalibracyjnych, dla rożnych materiałów lub różnych mieszanek i wybranie ich w prosty sposób przez operatora,
- oszczędności płynące z optymalizacji procesu suszenie lub zmniejszenia zużycia wody,
- możliwość rejestracji danych.
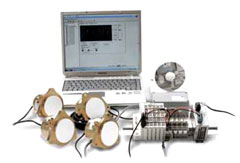
Cyfrowy system kontaktowego pomiaru wilgotności DMMS marki ACO
Warto przy okazji zauważyć, że nawet najlepsze urządzenie jest bezużyteczne, jeżeli jest zainstalowane w niewłaściwym miejscu. Najważniejszym zagadnieniem dotyczącym czujników kontaktowych jest zatem znalezienie odpowiedniego miejsca montażu. Nasze doświadczenie wskazuje bowiem, że złe umiejscowienie czujników powoduje 85% problemów pomiarowych! Niektóre przykłady typowych punktów montażowych dla czujników wilgotności to: podajnik ślimakowy, podajnik taśmowy (poprzez zamontowanie czujnika na płozie), na wysypie, ścianie silosu, boczniku.
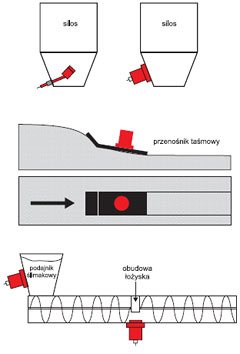
Przykładowy montaż czujników w silosie, podajniku taśmowym i ślimakowym
System oparty o czujniki kontaktowe do pomiaru wilgotności materiałów sypkich w zakresie określania i kontrolowania wilgotności jest już stosowany w następujących sektorach przemysłu:
betoniarski, szklarski, ceramiczny, spożywczy, chemiczny, biotechnologiczny (biomasa). System mierzy między innymi piasek, piasek kwarcowy, wapno, żwir, rudy, osadu ściekowe, zboża, kruszywa do betonu, biomasa (trociny, słoma, zrębki), ryż, gips, glina itp.
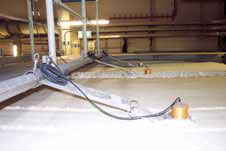
Pomiar gipsu na taśmociągu w trzech punktach
Mimo tego, że system kontaktowy jest relatywnie ekonomicznym rozwiązaniem, należy pamiętać o jego ograniczeniach, takich jak:
- zakres temperatury 4-100oC (brak pomiaru gdy w mierzonym materiale znajdują się kryształki lodu),
- maksymalna granulacja materiału do 8 mm,
- materiał nie może wykazywać tendencji do oklejania czujnika,
- warstwa nasypowa materiału na taśmociągu to minimum 5 cm (lub możliwość zastosowania kryzy spiętrzającej).
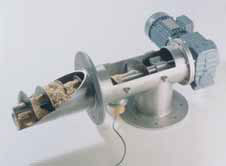
Pomiar trocin za pomocą podajnika ślimakowego montowanego na przesypie
3 METODY DLA ROŻNYCH ZASTOSOWAŃ
Wszystkie trzy omówione metody pomiaru wykorzystują inne zjawiska fizyczne w określaniu wilgotności materiału sypkiego. Różnią się także złożonością układu, stawianymi przed nimi wymaganiami prawnymi, dokładnością czy samymi możliwościami montażu. Dobór odpowiedniej metody nie jest więc kwestią prostą, jednakże mamy nadzieję, że niniejszy artykuł przybliżył Państwu nieco tę złożoną problematykę.
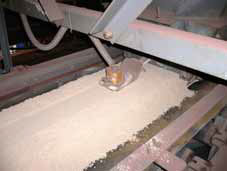
Przykładowy montaż czujnika na taśmociągu przy użyciu płozy