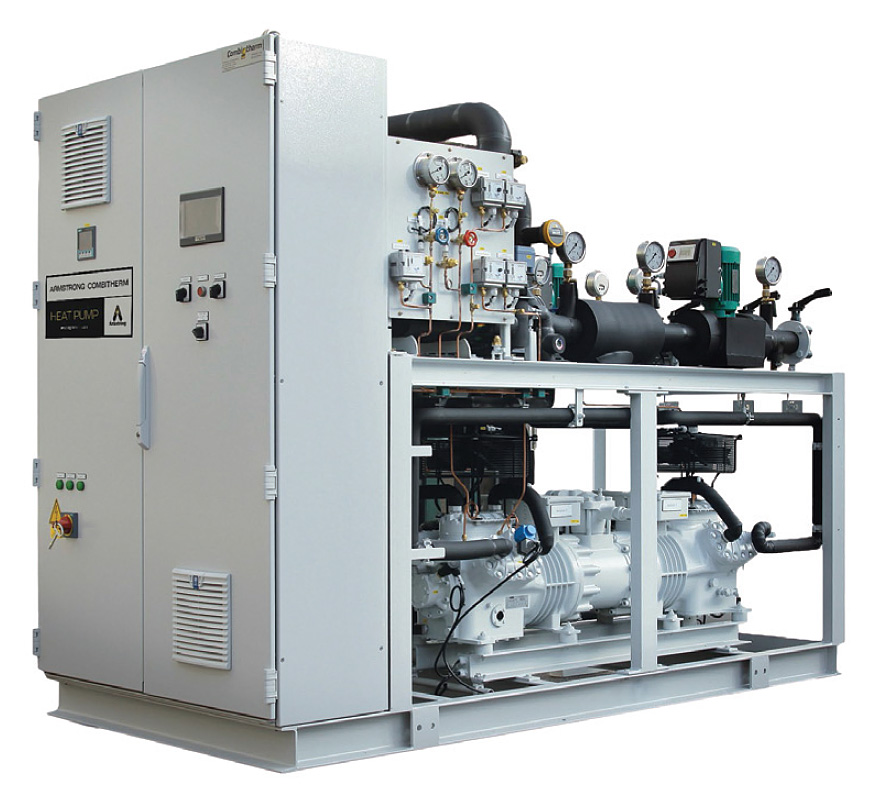
Każdy zakład produkcyjny wykorzystuje dużą ilość energii, która dostarczana jest w postaci energii elektrycznej i paliw kopalnych. Zazwyczaj 20% energii przychodzącej wykorzystywana jest do oświetlenia oraz do urządzeń zamieniających energię elektryczną w mechaniczną. Czy w takim razie to oznacza, że 80% energii pierwotnej wykorzystywana jest w procesie wytwarzania? W większości branż przemysłowych niestety odpowiedź jest jednoznacznie przecząca. Otóż tylko niewielka część energii wykorzystywana jest w produkcie końcowym, a olbrzymie ilości energii pierwotnej kończą jako ciepło odpadowe, często tracone kominami, wieżami chłodniczymi czy ściekami. To właśnie w cieple odpadowym należy szukać wymiernych i często ogromnych oszczędności dla zakładu i korzyści dla naszej planety.
PROCESY GRZANIA I CHŁODZENIA W PRZEMYŚLE
Następujące po sobie procesy grzania i chłodzenia stanowią podstawę wytwarzania produktów w przemyśle. Chłodzenie osiąga się poprzez usuwanie ciepła z cieczy, w specjalnie zaprojektowanych wieżach chłodniczych, z których zazwyczaj wydobyte ciepło ulatnia się do atmosfery. Są to olbrzymie ilości energii, które mogą stanowić aż 1/3 zapotrzebowania zakładu w ciepło. Największy potencjał ciepła odpadowego z chłodzenia występuje w fabrykach, które stosują procesy głębokiego zamrażania, a wytworzone produkty opuszczają fabrykę w temperaturze niższej niż dostarczone do fabryki surowce.
Głównie są to producenci lodów czy mrożonek.
Z kolei w procesach grzewczych ciepło tracone jest do atmosfery w wyniki nieefektywności w wytwarzaniu i dystrybucji mediów. Warto tu nadmienić zakłady, w których wykorzystywana jest para wodna jako źródło ciepła, a ich efektywność systemu parowego na ogół waha się między 60 a 80%. Energia wykorzystywana jest do procesów takich jak: suszenie produktów poprzez odparowanie wody, podgrzewanie produktu w celu wywołania reakcji chemicznej, ogrzewanie, nawilżanie, osuszanie powietrza, podgrzewanie wody służącej do mycia itp. No właśnie, a co dzieje się z energią w kolejnym etapie? W procesach suszenia, które stanowią największe zużycie pary, aż 80% energii uwalniana jest do atmosfery poprzez kominy w postaci bardzo wilgotnego powietrza o temperaturze poniżej 80°C. W kolumnach destylacyjnych czy wyparkach dzieje się podobnie, bo produkt końcowy również musi być schłodzony.
Rysunek nr 1 przedstawia typowy (niestety) przepływ energii w fabryce.
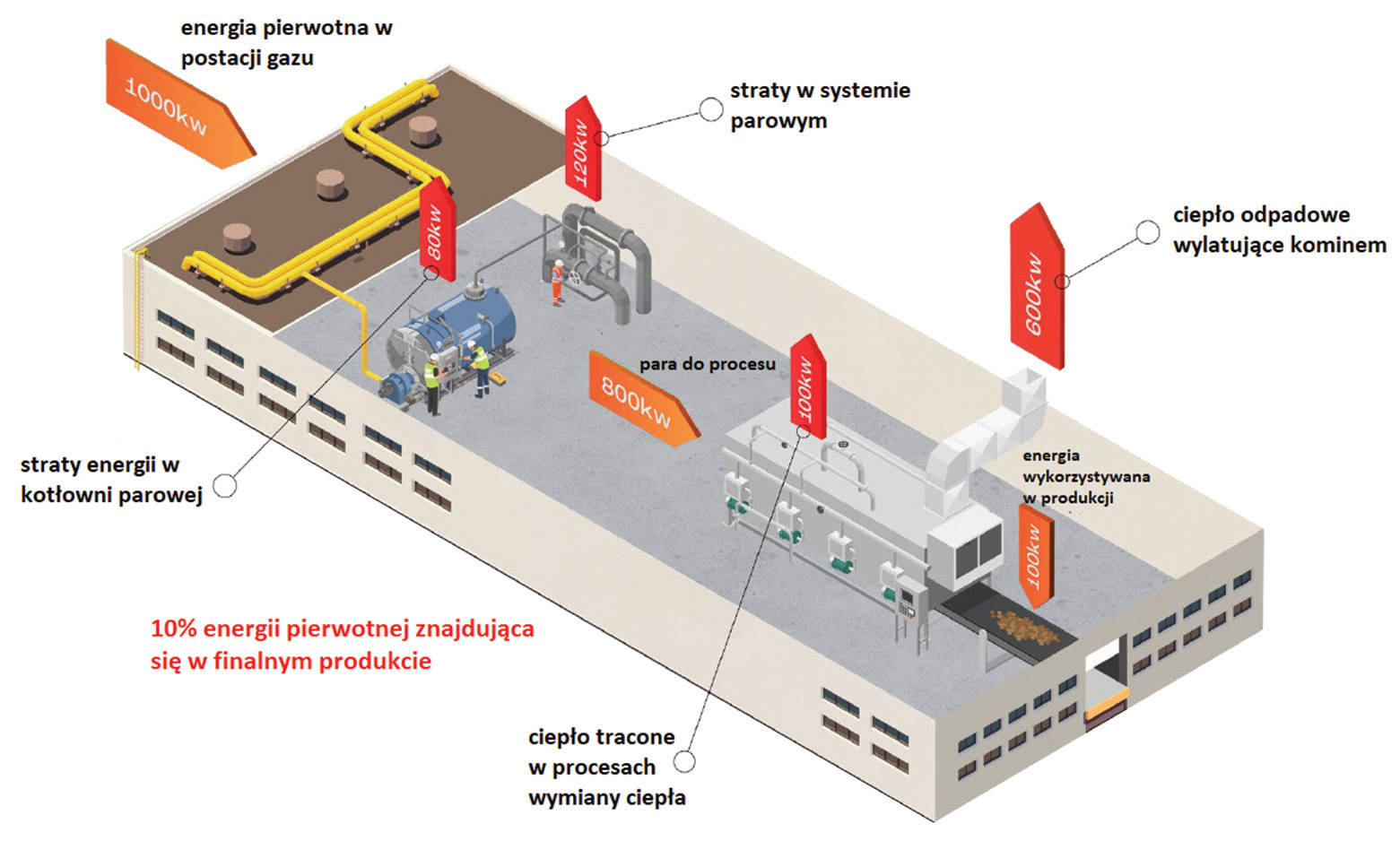
Rysunek 1.
Straty energii pierwotnej w typowym zakładzie przemysłowym
WYKORZYSTANIE ENERGII W OBIEGU
Mimo, że wartości energii w cieple odpadowym znacząco są mniejsze w stosunku do energii pierwotnej, to jej ilość nadal jest znacząca. Szacuje się, że 50 do 80% energii wykorzystywanej w przemyśle lekkim tracona jest w postaci ciepła w temperaturze poniżej 200°C lub nawet w temperaturach poniżej 90°C. Oznacza to, że powyższe 50 do 80% energii może być powtórnie wykorzystane. Ba! Stosując cyrkulację ciepła przemysłowego możemy sprawić, że będzie ono wykorzystywane powtórnie w procesie. W celu uzyskania maksymalnej efektywności energetycznej zakładów przemysłowych stosuje się analizy integralności procesów lub metody analityczne określane jako „Pinch”. Metoda Pinch polega na mapowaniu zimnych i gorących strumieni celem oszacowania, jaką maksymalną ilość ciepła możemy odzyskać, przy minimalnym zapotrzebowaniu na energię w fabryce. Inaczej mówiąc, procesy zachodzące w przemyśle oparte są na grzaniu bądź na chłodzeniu. Metodologia Pinch polega na wytyczeniu dwóch krzywych reprezentujących te procesy i znalezieniu punktu, w którym te krzywe są najbliżej siebie, czyli miejsca, w którym będzie najmniejsza temperatura różnicowa między nimi.
Przebiegi strumieni pokazano na rysunku nr 3.
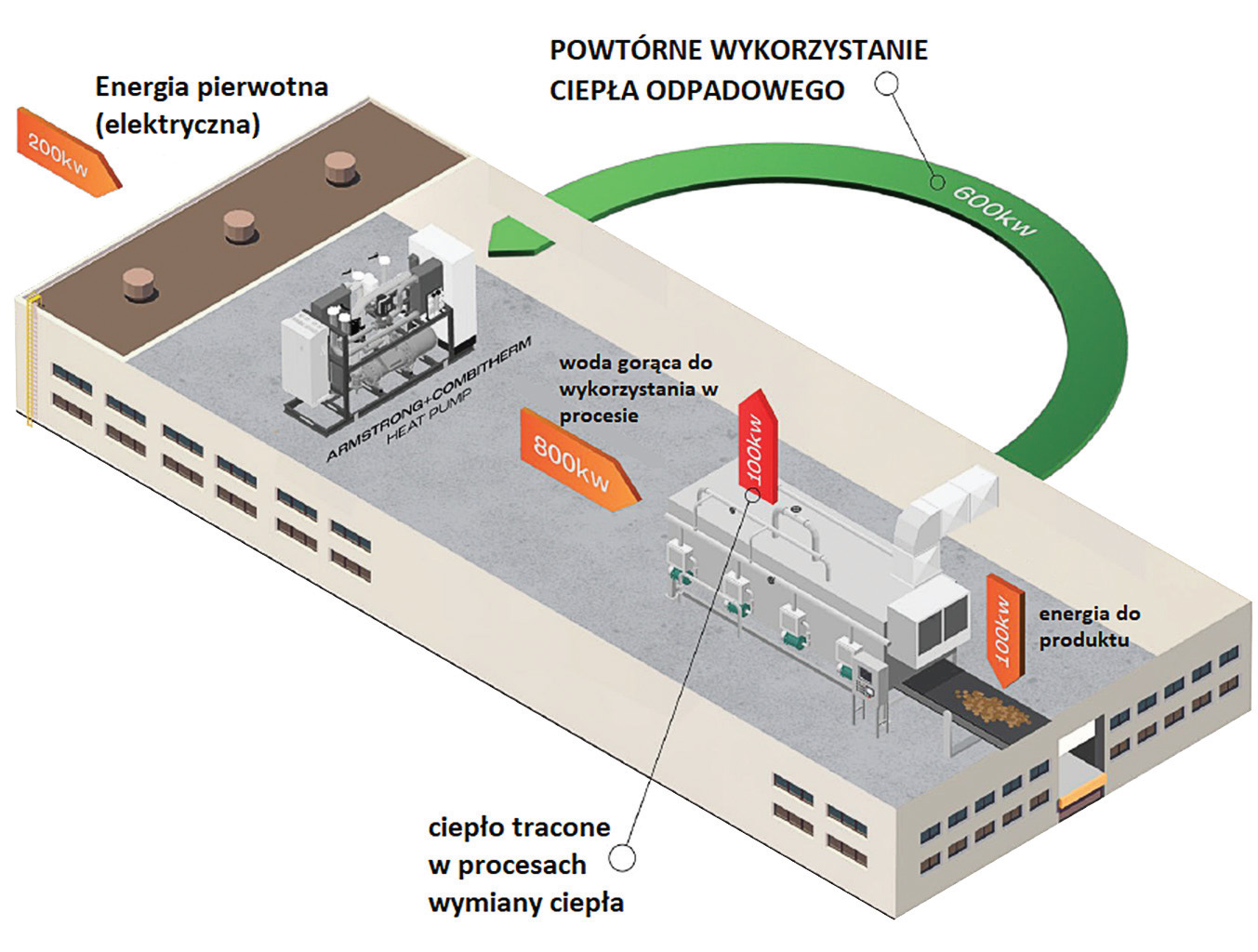
Rysunek 2.
Powtórne wykorzystanie ciepła odpadowego przy wykorzystaniu pompy ciepła
W punkcie Pinch potrzebujemy użyć najmniej energii do podgrzewania zimnej krzywej przez wymianę ciepła pomiędzy procesami. W przemyśle lekkim do odzyskiwania i magazynowania ciepła odpadowego z procesów chłodzenia wykorzystywana jest sieć wymienników ciepła. Efektem finalnym jest zmniejszenie zużycia energii pierwotnej i emisji CO₂. Stojąc w obliczu galopujących cen energii i konieczności dekarbonizacji, jeden ze światowych liderów wspierających zakłady przemysłowe w epoce przemian, firma Armstrong International, swoją mapę drogową rozbija na trzy etapy:
- Optymalizacja wydajności systemu poprzez wykorzystanie ciepła odpadowego.
- Zminimalizowanie zapotrzebowania na energię w procesie.
- Dekarbonizacja głównego źródła energii.
Przyjrzyjmy się tym etapom.
ETAP 1.
OPTYMALIZACJA WYDAJNOŚCI SYSTEMU POPRZEZ WYKORZYSTANIE CIEPŁA ODPADOWEGO
W Polsce wciąż mamy wiele zakładów powstałych w słusznie minionej epoce, w której paliwa kopalne uważano za tanie i łatwo dostępne źródło energii. Niewielu wtedy przejmowało się również emisją CO₂, więc projektowanie było łatwe i jednokierunkowe, tj. ciepło odpadowe ulatniało się na ogół kominem i mało kto się tym przejmował. Dzisiejsze realia spowodowały diametralną zmianę. Obecnie, w obliczu wojny za naszą wschodnią granicą, dostęp do energii, a raczej jej brak ma charakter geopolityczny. To sprawia, że energia odnawialna staje się relatywnie tańsza, zważywszy, że koszty emisji CO₂ są coraz większe. Zresztą ceny emisyjności CO₂ w Polsce są jedne z najwyższych w całej Unii Europejskiej ze względu na udział paliw kopalnych w procesie wytwarzania energii. Przyszedł zatem czas, że i z punktu widzenia ekonomii, przemiany stają się opłacalne.
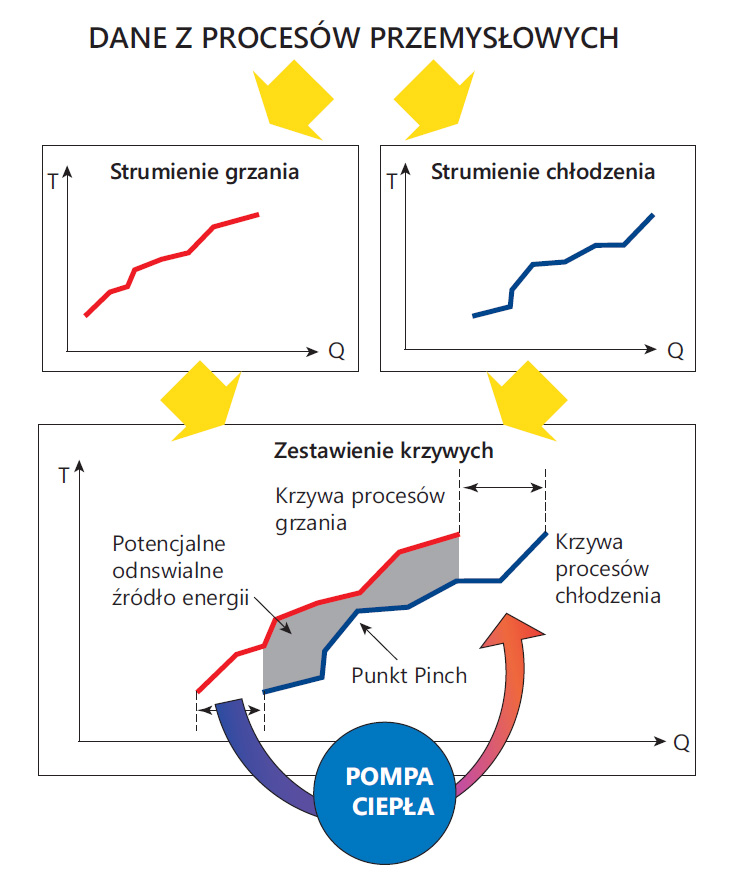
Rysunek 3.
Zestawienie strumieni grzania i chłodzenia celem określenia punktu Pinch
Wróćmy jednak do wykorzystania ciepła odpadowego. W momencie całkowitego zniknięcia paliw kopalnych z procesu wytwarzania energii, najbardziej ekonomicznym sposobem pozyskiwania energii będzie cyrkulacja energetyczna i dekarbonizacja systemu.
PROCES ODEJŚCIA OD PARY WODNEJ
Fabryki wykorzystujące parę w przemyśle lekkim z reguły wytwarzają i dystrybuują parę nasyconą o ciśnieniu 10 bar w temperaturze 185°C, nawet jeżeli sam proces wymaga dużo niższej temperatury. W aspekcie cyrkulacji energii, odzyskiwanie ciepła odpadowego do wytwarzania pary o niskim ciśnieniu, którą można następnie sprężyć do wyższego ciśnienia, jest technicznie wykonalne. Jeśli jednak ostatecznym celem jest podgrzanie produktu w znacznie niższej temperaturze, spowoduje to nadmierne zużycie energii, częściowo ze względu na minimalne 20% straty, które powszechnie akceptowalne są w systemach parowych. Innymi słowy jest to nieopłacalne.
Odparowanie ciepła powinno być wykorzystane do ogrzewania niskotemperaturowego.
Dlatego jedynym kierunkiem jest odejście od pary wodnej (z ang. desteaming), wykorzystanie wody jako czynnika grzewczego w temperaturze do 120°C i optymalizacja procesu odzysku ciepła odpadowego. Mówiąc ściślej, proces wytwarzania ciepła i wykorzystania go w procesie musi się zazębiać, a odparowanie ciepła powinno być wykorzystane do ogrzewania niskotemperaturowego. Teoretycznie, zerkając na tabele parowe zauważymy, że korzystanie z gorącej wody wymaga znacznie większych powierzchni wymiany ciepła, ponieważ ciepło jawne zawiera od 4 do 5 razy mniej energii niż ciepło utajone. Jednakże w praktyce, wykorzystywane wymienniki parowe są często przewymiarowane, dlatego kalkulacje wskazują, że często wystarczające jest podwojenie powierzchni wymiany ciepła.
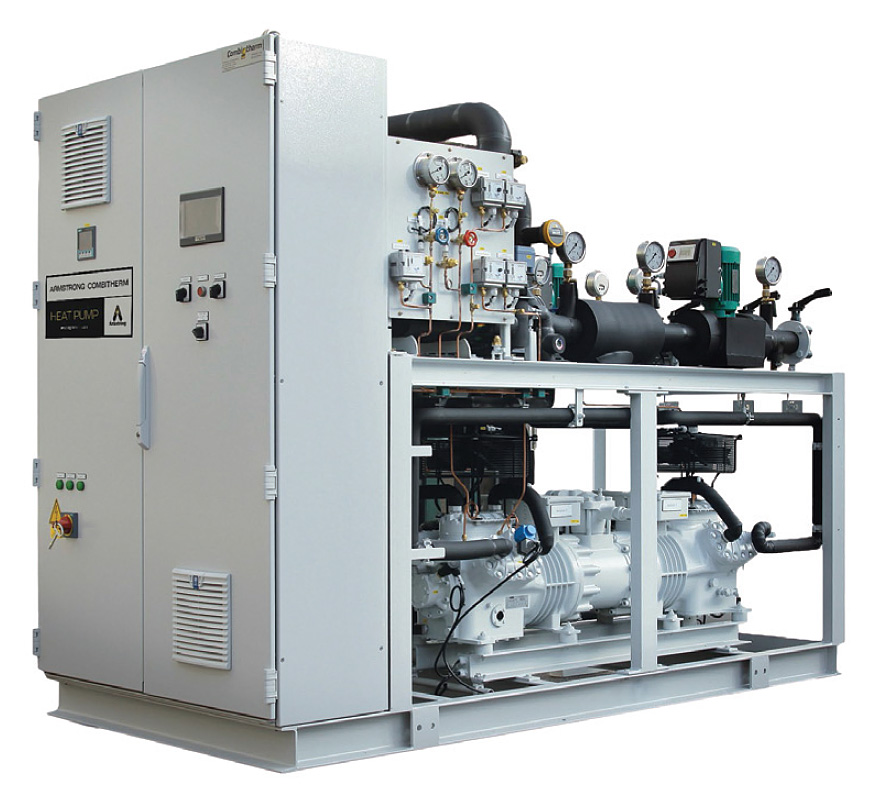
Rysunek 4.
Przemysłowa pompa ciepła Armstrong
POMPA CIEPŁA, CZYLI SERCE NOWOCZESNEJ FABRYKI
Ciepło odpadowe z procesów grzewczych często można odzyskać jedynie za pomocą wymienników ciepła. Jeżeli powietrze procesowe jest zanieczyszczone, może to być niezwykle trudne do przeprowadzenia. Ponadto, ciepło odpadowe jest często dostępne w temperaturach niższych niż wymagania procesu, dlatego jego parametry muszą być podwyższane. Tu swoją rolę odgrywa pompa ciepła. Przy wykorzystaniu energii elektrycznej uruchamiane są kompresory pompy, których zadaniem jest zwiększenie temperatury ciepła odpadowego do wymaganych poziomów.
Odzyskane ciepło krążące w cyrkulacji w dowolnym momencie może zostać wykorzystane do procesu podwyższania temperatury ciepła odpadowego i rozprowadzania go do odbiorników energii.
Technologia stosowana w pompach ciepła istnieje przeszło od 170 lat. Jest to ta sama technologia, która obsługuje lodówki w naszych domach i klimatyzację w naszych biurach. Opiera się na krążącym czynniku roboczym – chłodziwie, które na przemian paruje i skrapla się. Inaczej mówiąc, pompę ciepła można najprościej określić jako urządzenie, w którym ciepło przenoszone jest poprzez pompowanie czynnika roboczego pomiędzy dwoma wymiennikami ciepła w cyklu parowania i kondensacji. Czynnik roboczy pompy wpływa do niskotemperaturowego wymiennika ciepła lub parownika, gdzie następuje odparowanie pod niskim ciśnieniem i pochłaniane jest ciepło ze źródła ciepła (proces absorbcji). Źródłem może być schłodzona woda wieży chłodniczej, czy dowolne stałe ciepło odpadowe.
W kolejnym etapie czas na sprężarkę, dzięki której zwiększa się ciśnienie i temperatura czynnika roboczego do wymaganej temperatury skraplania. Następnie czynnik roboczy wpływa do wysokotemperaturowego wymiennika ciepła w formie wysokotemperaturowego gazu. Tam oddaje pochłonięte wcześniej ciepło do odbiornika ciepła poprzez kondensację pod wysokim ciśnieniem, czego efektem jest ciecz o wysokiej temperaturze lub gorąca woda. Najważniejszą zaletą pomp ciepła jest ich wydajność. Energia elektryczna konieczna do zasilania pompy zazwyczaj stanowi tylko 25–30% całkowitego zużycia energii. Co więcej, prawie cała ta energia ostatecznie przekształcana jest w ciepło użyteczne. Ważne przy tym jest to, że większość energii wyjściowej z pompy pochodzi z odzyskanego ciepła odpadowego o niskich parametrach.
Najczęściej pompy ciepła wykorzystywane w obiegu zamkniętym w przemyśle lekkim są o średniej mocy, oscylującej między 0,5 MW a 2 MW na jednostkę. Stosuje się w nich różnego typu czynniki robocze, które powinny być bezpieczne dla środowiska i niezawodne (ze względu na stosunkowo niskie ciśnienie w obiegu). Poprzez cyrkulację i przemiany termodynamiczne ich zadaniem jest zwiększenie temperatury ciepła odpadowego niższego niż 80°C do temperatury 120°C. Ten poziom temperatury umożliwia dodatkowo, w razie konieczności, wytworzenie pary o niskim ciśnieniu. Para ta może być wykorzystana do bezpośredniego wtrysku w produkt w procesie produkcyjnym lub, za pomocą termokompresorów, można zwiększyć jej temperaturę i ciśnienie.
MAGAZYNOWANIE CIEPŁA ODPADOWEGO
Ciepło odpadowe nie zawsze jest dostępne wtedy kiedy jest potrzebne. Po jego odzyskaniu gdzieś musi być dostarczone i przechowywane – zwykle w postaci gorącej wody do czasu, aż będzie można ją wykorzystać w procesie. Wyzwanie może stanowić konieczna do tego odpowiednia powierzchnia w fabryce, a to często bywa trudne. Dzięki zastosowaniu pomp ciepła i obiegowi energii uzyskuje się bardziej dynamiczny system. Odzyskane ciepło krążące w cyrkulacji w dowolnym momencie może zostać wykorzystane do procesu podwyższania temperatury ciepła odpadowego i rozprowadzania go do odbiorników energii. Jest to bardzo wygodne również z punktu widzenia oszczędności, gdyż pompy mogą pracować w momencie najtańszej energii elektrycznej.
System jest na tyle zautomatyzowany, że wykorzystując dane w czasie rzeczywistym decyduje, kiedy ciepło powinno być transportowane, a kiedy magazynowane.
ETAP 2.
MINIMALIZOWANIE ZAPOTRZEBOWANIA NA ENERGIĘ W PROCESIE
Stosunek ilości energii elektrycznej zużywanej przez pompę do dostarczanego ciepła określa współczynnik wydajności COP (z ang. Coefficient of Performance). Im COP jest większy, tym uzyskanie tej samej ilości ciepła wymaga mniejszego nakładu energii elektrycznej. Co oczywiste, COP związany jest więc ze wzrostem temperatury ciepła odpadowego. Optymalizacja współczynnika COP jest głównym powodem wyznaczania punku Pinch, by źródła ciepła i temperatury grzania były
względem siebie tak blisko, jak to możliwe.
Dotychczas projektowanie wielu procesów opierało się na wyższych temperaturach użytkowych, w których stosunkowo łatwo jest je uzyskać stosując parę wodną jako czynnik grzewczy. Natomiast analizując rzeczywistą temperaturę pary w wymienniku ciepła (po obniżeniu ciśnienia przez zawór regulacyjny), czy wgłębiając się w wymogi temperaturowe procesu okazuje się często, że wymagana temperatura grzania jest znacznie niższa. W wyniku optymalizacji systemu opartym na analizie Pinch, współczynnik COP poprawia się nie wpływając na warunki procesowe w fabryce. Co ważne, pompy ciepła wytwarzające niższe temperatury wyjściowe wymagają mniej energii elektrycznej, więc współczynnik COP jest wyższy.
ETAP 3.
DEKARBONIZACJA ŹRÓDEŁ ENERGII W FABRYCE
Energia elektryczna jest konieczna do uzyskania cyrkulacyjnego obiegu energii w zakładzie. Mówiąc o dekarbonizacji, należy pozyskać energię z odnawialnych źródeł energii. Tak więc pod rozwagę należy wziąć źródła takie jak energia słoneczna, wodór, biogaz, czy biomasa. Firma Armstrong International podkreśla, że etap ten powinien zostać przeprowadzany na samym końcu, po procesie optymalizacji i osiągnięciu minimalnego zapotrzebowania na energię.
KLUCZOWE ZALETY SYSTEMU OBIEGU CIEPŁA
Dzięki zastosowaniu obiegu ciepła w przemyśle możliwe jest odzyskanie bardzo dużej ilości energii cieplnej. Co więcej, metodologia ta nie powinna ograniczać się do granic poszczególnych fabryk, ale tworzyć wspólny sąsiedzki system. Podczas gdy coraz większa liczba obszarów przemysłowych stosuje podejście obiegowe w stosunku do materiałów i wytwarzania energii, to wciąż rzadkością jest dzielenie się i uzdatnianie ciepła odpadowego w sąsiadujących zakładach przemysłowych. Wraz z rozwojem przenośnych magazynów energii poszerzają się możliwości przepływu ciepła odpadowego na średnie odległości (najlepiej przy wykorzystaniu transportu niskoemisyjnego). Tak więc, zakłady przemysłu ciężkiego posiadające nadmiar wysokogatunkowego ciepła odpadowego mogłyby udostępnić go lekkim zakładom przemysłowym lub ciepłowni zlokalizowanej w zupełnie innej miejscowości.
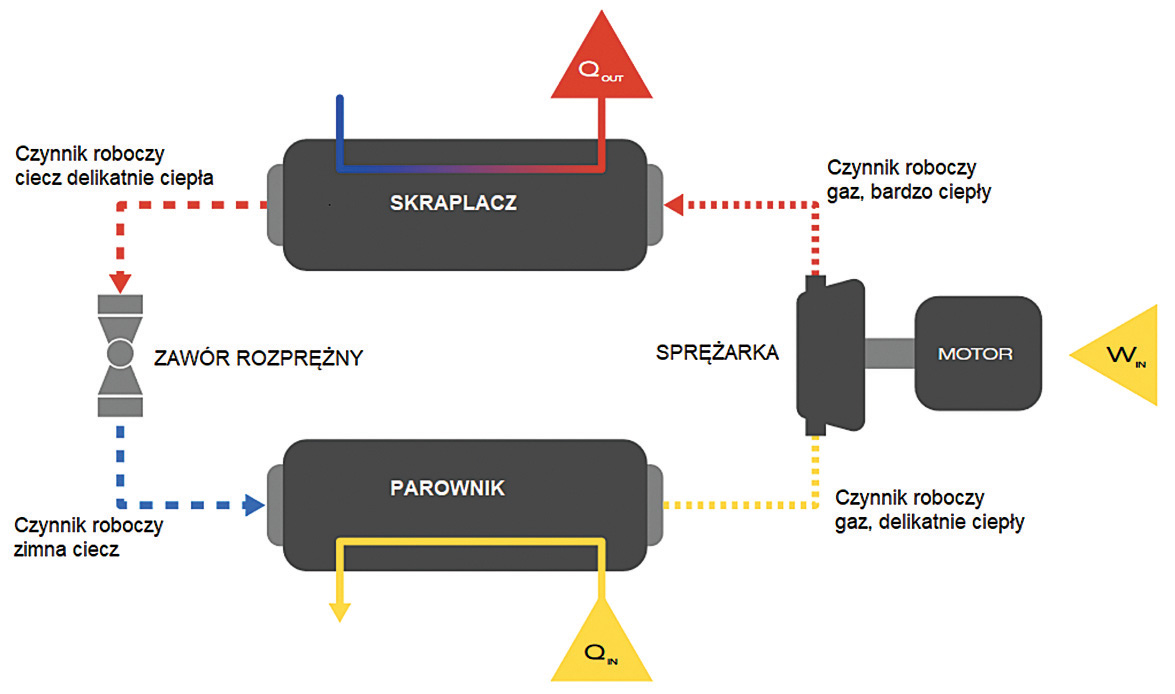
Rysunek 5.
Schemat działania pompy ciepła
POTENCJAŁ OGRZEWANIA I CHŁODZENIA BUDYNKÓW PRZY WYKORZYSTANIU CIEPŁA ODPADOWEGO
Odzyskiwane ciepło odpadowe można również ponownie wykorzystać do ogrzewania i chłodzenia budynków. Jednak zastosowanie systemu obiegu ciepła stanowi większe wyzwanie w budynkach niż w przemyśle – ze względu na czas i zachodzące procesy. Aplikacje w przemyśle wymagają bowiem regularnego ogrzewania i chłodzenia, przynajmniej w odstępie jednego tygodnia.
Odzyskując i ponownie wykorzystując ciepło w zakładach przemysłowych możemy znacząco zmniejszyć trudność dekarbonizacji i ilość energii wymaganej do działania fabryk w przyszłości.
W przypadku obiegu ciepła w budynkach, ze względu na zmieniające się pory roku, musiałyby powstać magazyny ciepła, które utrzymywałyby temperaturę ciepła na podobnym poziomie na okres powiedzmy 6 miesięcy. Jeśli pewnego dnia powstaną niedrogie magazyny ciepła, wówczas znacząco wzrośnie współczynnik COP pomp ciepła i kierunek ten nabierze sensu.
ODZYSKIWAĆ ENERGIĘ, REDUKOWAĆ KOSZTY, CHRONIĆ ŚRODOWISKO
Procesy ogrzewania i chłodzenie w przemyśle, tak jak i budynkach, odpowiadają za około 70% obecnego światowego zapotrzebowania na energię. Odzyskując, ulepszając i ponownie wykorzystując ciepło w zakładach przemysłowych, możemy znacząco zmniejszyć trudność dekarbonizacji i ilość energii wymaganej do działania fabryk w przyszłości. Na całym świecie już teraz trwa transformacja istniejących obiektów, a coraz większa liczba nowych zakładów przemysłowych projektowana jest przy uwzględnieniu metodologii cyrkulacji energii. W istniejących zakładach natomiast trwałe obniżanie kosztów energii jest warte wysiłku, nawet w przy padkach, gdy wymagane są dodatkowe nakłady inwestycyjne (głównie w przypadku całkowitego odejścia od pary wodnej). Warto zaznaczyć także, że w dłuższej perspektywie czasu koszty operacyjne można jeszcze bardziej zmniejszyć poprzez stopniową wymianę urządzeń o lepszej efektywności energetycznej.
Rozpatrując kwestie odzysku ciepła pamiętać należy także o tym, że do 2050 roku gospodarka Unii Europejskiej ma być zeroemisyjna. Dlatego już teraz należy rozpocząć inwestycje w powtórne wykorzystanie ciepła odpadowego, tym samym zmniejszając emisję gazów cieplarnianych. To jedyna droga, którą cały świat musi podążać. Z uwagi na planetę, życie nasze i kolejnych pokoleń – oby to stało się jak najszybciej.