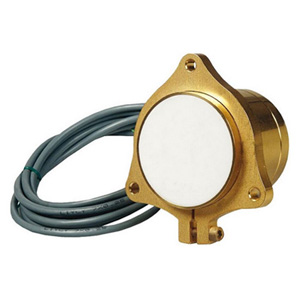
Producenci europalet zobligowani są do spełnienia surowych norm, potwierdzających trwałość i wysoką jakość gotowych produktów. Jednym z elementów kluczowych dla wytrzymałości każdej europalety są wsporniki, których właściwości podlegają ścisłej kontroli jakościowej. Na jakość wsporników wpływ ma kilka czynników, a jednym z głównych jest wilgotność materiałów używanych w procesie produkcji. Producenci europalet zobligowani są do spełnienia surowych norm, potwierdzających trwałość i wysoką jakość gotowych produktów. Jednym z elementów kluczowych dla wytrzymałości każdej europalety są wsporniki, których właściwości podlegają ścisłej kontroli jakościowej. Na jakość wsporników wpływ ma kilka czynników, a jednym z głównych jest wilgotność materiałów używanych w procesie produkcji.
Eko palety
Wsporniki to elementy konstrukcyjne w postaci klocków, łączące górną i dolną warstwę desek w paletach. W tradycyjnych paletach wsporniki wykonywane są z litego drewna pochodzącego ze ścinanych w lesie drzew. Pełnowartościowy materiał stanowiący cenny surowiec np. do produkcji meblarskiej, jest „marnowany” na mało efektowny półprodukt. Ponadto, wytrzymałość wsporników z litego drewna jest niska, szczególnie w przypadku niekorzystnych warunków atmosferycznych.
Zarówno względy ekologiczne, jak i czysto użytkowe przyczyniły się więc do wypracowania nowych technologii, które wykorzystuje nasz Klient – fabryka wsporników do europalet. Wsporniki wykonywane są z wiórów i trocin drzewnych, a więc z materiału odpadowego, który w najlepszym razie byłby spalany po przerobieniu na brykiety.
Proces produkcji wsporników rozpoczyna się od transportu przenośnikami ślimakowymi wiórów z pryzmy magazynowej do suszarni, gdzie usuwany jest nadmiar wilgoci. W zależności od rodzaju wiórów, zawartość wody w materiale powinna wynosić od kilku do maksymalnie kilkunastu procent. Następnie, do surowca drzewnego dodawane jest lepiszcze, całość jest mieszana i kierowana do form. W formach mieszanina jest prasowana i nadaje jej się kształt kostek o odpowiednich wymiarach.
Po sprasowaniu i sklejeniu, kostki są suszone i stają się gotowym elementem do produkcji europalet. Przepisy europejskie stawiają paletom wysokie wymagania. Wsporniki muszą posiadać dużą wytrzymałość mechaniczną, a także być odporne na wilgoć (często palety są składowane i używane w trudnych warunkach; na otwartym terenie bywają narażone na działanie wody). Z uwagi na rygorystyczne wymogi jakościowe, wsporniki poddawane są kontroli laboratoryjnej, która sprawdza ich odporność mechaniczną i wodoodporność. W tym celu są one zgniatane w prasie określającej ich wytrzymałość. Odporność na zawilgocenie sprawdza się przez długotrwałe zanurzanie gotowych wsporników w wodzie. Jedynie produkty spełniające wymagania norm mogą być używane do konstrukcji europalet i w rezultacie uzyskać wymagane certyfikaty jakości.
Kluczowa jest wilgotność
Ważnym parametrem mającym wpływ na jakość końcowego produktu jest wilgotność podstawowego materiału używanego do produkcji wsporników, czyli wiórów i trocin. Zawartość wody w materiale kierowanym do form zasadniczo wpływa bowiem na proces zagniatania i sklejania kostek wsporników, a jedynie prawidłowo zagęszczone i sklejone wsporniki spełniają warunki określone w normach. Z tego względu linie produkcyjne powinny być wyposażone w niezawodne urządzenia do ciągłego pomiaru wilgotności trocin/wiórów. Optymalnym rozwiązaniem jest zastosowanie przyrządów umożliwiających także sterowanie procesem suszenia.
Kontaktowy DMMS
W fabryce wsporników naszego Klienta, wilgotność wiórów powinna być mierzona w czterech punktach linii produkcyjnej. W przypadku nowych rozwiązań pomiarowych lub nowych zastosowań, wskazane jest wykonanie odpowiednich prób, aby zapewnić pożądaną funkcjonalność układu. Dlatego też wstępnie zainstalowano jeden czujnik wilgotności DMMS, z możliwością łatwej rozbudowy systemu o kolejne 3, a nawet 15 czujników (podłączonych do jednej jednostki elektroniki). Odległość między modułem elektroniki, a czujnikami może wynosić standardowo do 600 m (przy zastosowaniu innego typu kabla nawet do 1200 m), co również miało istotny wpływ na wybór tego rozwiązania.
Ważnym faktem jest to, że pomiar jest kontaktowy i wymaga bezpośredniego styku czujnika z materiałem mierzonym. Układ z jednym czujnikiem miał posłużyć jako testowy w celu określenia optymalnych warunków montażu i pomiaru. Podstawowy problem, który trzeba rozwiązać w przypadku pomiaru takich materiałów jak wióry, trociny, sieczka słomiana itp. stanowi ich ściśliwość. Uzyskanie dokładnego i powtarzalnego wyniku wymaga, aby wszystkie mierzone partie materiału posiadały jednakową gęstość.
Innymi słowy, w momencie pomiaru, próbki mające kontakt z czujnikiem powinny być jednakowo ugniecione. Nie ma znaczenia stopień sprasowania materiału, istotne, aby był on za każdym razem taki sam – ważna jest powtarzalność. Problem jest istotny, gdyż niedotrzymanie powyższego warunku prowadzi do niedokładności wskazań rzędu 30%, a przy takim rozrzucie wyników pomiar traci sens.
Rozwiązaniem tego problemu jest umieszczenie czujnika w odpowiednim miejscu przenośnika ślimakowego. Ślimak urządzenia (śruba), transportując materiał, dokonuje jego zagęszczenia, ugniatając wióry jednakowo z taką samą siłą. Z punktu widzenia zapewnienia optymalnych warunków prowadzenia pomiaru wilgotności, najlepszym miejscem dla czujnika jest okolica wylotu, gdzie materiał jest bliski opuszczenia przenośnika. W instalacjach, w których trociny lub wióry transportuje się inaczej niż ślimakiem (np. pneumatycznie lub przenośnikiem kubełkowym, zgarniakowym itp.), dostarczany może być opcjonalnie krótki przenośnik ślimakowy z zamontowanym czujnikiem. W takim przenośniku czujnik zamontowany jest w obudowie pionowo od spodu. Kierując się tym przykładem, w zakładzie naszego Klienta, czujnik zamontowano pierwotnie w obudowie przenośnika ślimakowego, od dołu.
W czasie prób okazało się jednak, że to usytuowanie czujnika powoduje niedokładności pomiaru bądź jego zawieszanie się. Przyczyną było gromadzenie się najdrobniejszych frakcji materiału na czujniku. Przesuwany ślimakiem materiał nie zabierał bowiem wszystkich wiórów z powierzchni czujnika, a pozostała, cienka warstwa powodowała problemy pomiarowe.
Musieliśmy znaleźć inne miejsce optymalnego montażu. Czujnik został umieszczony w pozycji „godzina 17”, co spowodowało grawitacyjne osuwanie się resztek materiału z czujnika i zapewniło kontakt jego powierzchni czołowej z nowymi partiami mierzonego materiału. Inny problem pomiarowy wynikał z różnic w ugnieceniu materiału. Czujnik był zainstalowany przy końcu przenośnika, jednak w pewnej odległości od jego wylotu. Zgodnie z zasadą montażową, na odcinku nad czujnikiem, pióro ślimaka zostało nieco zeszlifowane aby zmniejszyć oddziaływanie metalu na czujnik. Z nieustalonych powodów materiał nie ulegał jednak powtarzalnemu zagęszczaniu. Kolejny raz czujnik został przesunięty w inne miejsce. Tym razem przy samym wylocie przenośnika, tuż za miejscem, w którym kończył się ślimak, w dalszym ciągu w pozycji „godzina 17”. W tym miejscu przekrój obudowy ulegał zwężeniu z powodu kołnierza, za pomocą którego jeden moduł obudowy łączył się z kolejnym. To zwężenie powodowało gromadzenie się i ugniatanie materiału dostarczanego i pchanego przez ślimak. Nowa pozycja czujnika okazała się idealna. Uzyskano bardzo stabilne i powtarzalne wyniki pomiaru.
Kalibracja układu
Mając pewny i wiarygodny pomiar wilgotności, należało w sposób właściwy wykalibrować urządzenie. Kalibracja czujnika DMMS polega na kolejnym transportowaniu przez przenośnik z zamontowanym czujnikiem minimum dwóch partii mierzonego materiału o różnej wilgotności, najlepiej o wartościach zbliżonych do wartości skrajnych zakresu pomiarowego. Faktyczną zawartość procentową wilgoci w każdej próbce oznacza się przy pomocy wagosuszarki.
W trakcie przejścia przez linię próbki kalibracyjnej, czujnik określa bezwymiarową wartość cyfrową wilgotności każdej próbki. Następnie, w programie, wartości cyfrowej przypisuje się zmierzoną wilgotność w procentach. Mając minimum dwie zależności wartość cyfrowa – wartość procentowa wilgotności, program wykreśla krzywą kalibracyjną, według której następnie wykonywane są pomiary wilgotności materiału.
Po wykalibrowaniu czujnik jest gotowy do pracy. W zależności od posiadanych wyjść sygnałowych elektroniki i ich konfiguracji, zmierzone wartości można wyświetlić na prostym, dodatkowym wyświetlaczu, bądź przesłać do systemu nadrzędnego i wykorzystać do sterowania procesem technologicznym.
Ostateczne testowanie
Po wykonaniu wszystkich czynności, rozpoczęto normalną pracę linii produkcyjnej. Zainstalowany system pomiaru wilgotności DMMS został poddany próbom eksploatacyjnym, od wyniku których Klient uzależnił nabycie kolejnych trzech czujników. Próby trwały około miesiąca.
Na tym etapie testu układ pomiarowy nie został wykorzystany do automatycznego sterowania procesem produkcyjnym, jednak stwierdzono, iż ciągły, wystarczająco dokładny pomiar wilgotności z wizualizacją wyników bardzo ułatwia ręczne prowadzenie procesu. Obsługa nie musi określać „na oko” wilgotności wiórów i w konsekwencji, w stosunkowo łatwy sposób udaje się utrzymywać zawartość wilgoci w założonym przedziale. Dzięki pomiarowi i możliwości przewidywania trendów, można uniknąć stanów ekstremalnych, wymuszających gwałtowne reakcje obsługi (jak np. nagłe zwiększanie lub zmniejszanie intensywności ogrzewania suszarni).
W trakcie prób potwierdzono prawidłowość pracy całego cyfrowego systemu pomiaru wilgotności DMMS. Klient stwierdził przydatność tego pomiaru w fabryce i w efekcie, w niedługim czasie zamówił kolejne trzy czujniki. Dzięki doświadczeniu uzyskanemu w trakcie prób i wstępnego okresu eksploatacji, uruchomienie i kalibrację nowych urządzeń użytkownik mógł już wykonać we własnym zakresie.
Kolejne wyzwania
Instalacja DMMS w zakładzie wykorzystującym wióry do produkcji wsporników europalet jest największą do tej pory aplikacją cyfrowego systemu pomiaru wilgotności firmy ACO w kraju. Mimo początkowych trudności, udało nam się zrealizować system w pełni satysfakcjonujący naszego Klienta. Z naszej perspektywy wdrożenie to, mimo, iż pełne zaskakujących zwrotów sytuacji, było dla nas swoistym przetarciem ścieżek. Wnioski wyciągnięte w trakcie prób umożliwiły przyśpieszenie prac w kolejnych zakładach, a zdobyte doświadczenia pozwalają nam na realizacje układów pomiaru wilgotności w innych aplikacjach, wykorzystujących materiały sypkie w procesach.